Characteristics of Thermocouples
Standardized Thermocouple Types
In the United States, nine material combinations presently are letter-designated by the American Society for Testing and Materials (ASTM) as thermocouple types: B, C, E, J, K, N, R, S, and T. Representative properties of letter-designated thermocouples are summarized in Table 1. To view that Table, Please Follow the Link. They are specialized for use in different temperature ranges and environments.
For U.S. standards, Seebeck characteristics are experimentally determined by the National Institute of Standards and Technology (NIST) from samples of the same nominal thermoelement material type provided by several manufacturers. Then, the independent standardizing committee, ASTM, with volunteer members representing manufacturers, calibrators, NIST, and users, prepares a consensus standardizing document based on the NIST data.
The standards committee adds commercial tolerances and application recommendations. The standards are only sanctioned by the American National Standards Institute (ANSI). From measurements at intrinsic standard reference temperatures, NIST defines the Seebeck characteristics, emfs, and coefficients, by E(T) polynomial functions of degrees between 8 and 14, rather than by the tabulated values. NIST then derives the corresponding inverse T(E) values, determined from E(T) by iteration.
For application convenience, NIST also presents polynomials of lower degree that approximate the actual characteristics over narrower temperature ranges. Properties of most letter designated types are published in NIST Monograph 175.
Significantly, it is the relative Seebeck characteristics rather than the material compositions or alloy names that are standardized. The specific alloy composition and metallurgical treatments of actual thermoelements may be varied, as for improved stability, so long as the pair initially conforms to the standard within tolerance.
For example, the nominal alloy composition used for EN and TN legs is slightly different from JN thermoelements that share the same alloy name (“Constantan”). Therefore, individual thermoelements should be used as selectively paired for thermocouples by the producer. Randomly paired thermoelements of the same letter-designated type from the same or different manufacturers or batches are not assured to conform to neither standardized paired characteristics nor tolerances.
Any thermocouple exposed to excessive high temperature for durations longer than a few weeks might progressively exceed the initial tolerance. (Such thermocouple “drift,” incorrectly viewed as global “de-calibration,” is from progressing local inhomogeneity.) The letter designation is complemented by suffixes.
A first suffix P or N, as in thermoelement types KP or KN of a thermocouple Type K pair, distinguishes positive from negative thermoelements. An added final X suffix distinguishes corresponding-type extension-grade wire material, as in KPX for a positive Type K extension thermoelement or KX for an extension-grade pair. (Some manufacturers distinguish compensating-type extensions by a nonstandardized C final suffix.)
Thermoelement extension-grade wire has the same nominal Seebeck coefficient as the nominal thermocouple type over some temperature range around ambient temperature but has a broader standardized tolerance than thermocouple-grade material.
Color Codes
Both thermocouple letter type and thermoelement polarity should be visually distinguishable. Seebeck emfs, coefficients, letter designations, and tolerances of the thermocouple types as standardized in the United States are essentially the same in many international standards.
Therefore, it is now functionally possible, but very inadvisable, to intermix in a circuit thermoelements of a particular type made to different standards and marked with multiple conflicting color codes. Unfortunately, the color codes used to identify these few types in different standards are inconsistent in every possible way. The unfortunate Babel of national color codes that presently exists is displayed in Table 2. To view that Table, Please Follow the Link.
American-standardized color codes used in the United States and Canada have remained fixed for many decades. Therefore, color code confusion of material types in the United States is mostly due to user error, carelessness, or, infrequently, to flawed coding or labeling in manufacture.
Now, from a single vendor, thermocouple materials are available made to several of the conflicting color codes. The disagreement between color codes could present a costly problem of misidentification, as of polarity. Circuits with multiple extension cables risk crossed-polarity error that may be hidden in thermometry.
In the U.S. thermocouple standards, uniquely, the negative thermoelement is always coded as red (unfortunately, contrary to other common U.S. electrical and instrument practices). This is also contrary to historic national thermocouple color codes of China, Germany, and Japan, in which red always designated the positive thermoelement.
The Japanese standard denotes thermocouple type only by overall jacket color with positive leg always red and negative always white. By U.K. standard, the negative leg of all letter-designated types is blue.
In France, the positive thermoelement is always yellow, but both Types E and K have the same yellow/purple wire in the French code with type distinguished by overall jacket color.
In English standards, yellow denotes only the positive Type JP material. In the U.S. standards, yellow marks only the KP thermoelement and Type K thermocouple material. The copper wire leads of some U.S. electric blasting caps use yellow insulated wire with a faint narrow parallel red tracer stripe that, in field use, has been confused with Type KX thermocouple extension wire.
The outer jacket of U.S. thermocouples is brown. Extension-grade material is distinguished by a jacket of the color of the positive thermoelement. An IEC standard provides for “intrinsic-safing” of instrumentation that must reside within a hazardous environment but be electrically isolated by electronic barriers from separated monitoring areas. (Intrinsic safety is not addressed in U.S. thermocouple standards.)
For uniform distinction of the intrinsic-safe class of application, even the low-voltage thermocouple circuits uniformly must be distinguished by a blue outer jacket. Special materials and electrical parameters may also be specified. Nevertheless, the thermoelectric characteristics of intrinsically safe and regular thermocouples are functionally identical. The user should confirm the material of each leg.
Thermocouple Selection
Thermocouple type selection is based on temperature range, compatibility with environment, sensitivity, wire size, cost, and user access to compatible indicators.
Temperature Range: Base-metal thermocouples cover the range from −200 °C to 1260 °C (Table 1). Higher temperatures require more expensive precious or refractory materials that extend the available upper limit to 1700 °C.
Environmental Compatibility: Potentially harmful environments are classified as oxidizing, oxygen-poor, neutral, vacuum, reducing, radiation, sulfurous, and so on. Thermocouples and sheaths react adversely to some environments depending on temperature range.
A thermocouple type is best suited for one or more of these environments but often is very unsuited to the others. An adverse environment locally introduces inhomogeneity into thermoelements and breaches protective sheaths.
Unfortunately, some environments alternate between incompatible conditions or simultaneously combine them. Thermocouple suppliers should be consulted for material recommendations for especially difficult situations that involve harsh chemical or radiation environments or mixed environments. Trial may be required.
Sensitivity: Relatively low emf once was a major limitation of thermocouples. Now, commonplace modern thermocouple monitoring instruments, in “open-circuit” (nulled-current) mode, can routinely indicate temperatures to 0.1°C or even 0.01°C resolution and stability with excellent noise rejection for all letter-designated thermocouple types. Thermocouple tolerances are much larger.
As seen in Table 1, the sensitivities of various types are very different. Precious and refractory metals have less than a quarter of the emf of the least sensitive Type N base-metal thermocouple.
Wire Size: Bare thermoelement material is readily available in diameters from 0.13 mm (0.0005 in.) to 3.3 mm (0.128 in.). Thermoelements of all diameters are sold separately or else matched as a thermocouple pair with standard tolerance. The finer wire sizes have less effect on the temperature being measured but degrade more quickly. Upper temperature limits vary with wire size (Table 3).
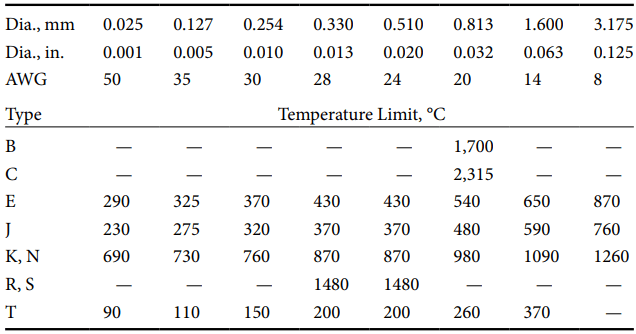
Fine wires are favored for transient thermometry, where space is limited, or for fine spatial resolution. Thermoelement resistance is not a factor in nulled-current thermometry. Some special applications favor thin foil or film thermoelements.
Cost: Thermoelement and thermocouple wire is available bare or in a wide variety of insulants ranging from vinyl, Kapton®, and Teflon® to glass or ceramic fiber with metal over-braid. The price varies irregularly with material and diameter.
Typically, the lowest price is for bare wire of mid-range diameters between 20 and 28 AWG. Price depends more on diameter than on material. The much larger and very fine diameter wires are more costly. Present unit price ranges widely between $0.24 and $5.28/ft over the range of available wire sizes.
Standardized Tolerances
ASTM standardized tolerances for as-manufactured thermocouple materials are established by committee formal consensus judgment of many experienced producers, users, and calibration standards laboratories staff.
Manufacturers characterize the Seebeck property typical of a production batch by calibration of one or more surrogate samples. Sampled first-cycle calibration is taken to be representative of all other thermoelements of the same batch. No authentic inhomogeneity tests are performed. Inhomogeneity has been shown usually to be well within tolerance for new material.
Once conformity to standardized tolerance is affirmed, rather than the specific calibration, the standardized type-characteristic is often attributed to the entire batch.
Standardized tolerances include not only overall deviation from the standardized Seebeck properties, but also cover inevitable small uncertainty from tolerable inhomogeneity and, in application, even possible irregular deviations, over small temperature spans, of user-simplified scaling relations from the standardized characteristic.
Tolerances apply only initially and briefly to material as delivered, not exposed to excessive temperature or adverse environments. The initial tolerances for standard letter-designated thermocouple types are presumed to be reliable until the thermocouples are exposed to an aggressive environment or for a few weeks at excessive temperature.
Thermocouple tolerances are additional to uncertainties of monitoring instruments and of thermal coupling and mass. There are separate initial tolerances for normal- and for special-grade material. Initial percent tolerances of ordinary material may be double or more of that of special-grade material. Yet the different degree uncertainty between commercial- and premium-grade tolerances is small and the cost premium is large (but less than the cost of individual calibration).
In severe use, special-grade materials can quickly degrade to exceed the initial tolerances of normal-grade material. Additionally, ASTM Standard E235-06 specifies special requirements for Types K or N thermocouples destined for nuclear or highreliability application.
Other Thermocouple Types
Standardized Non-Letter-Designated Thermocouples: Some less used commercial thermocouple pairs are for specialized use in thermometry. Some alloys are proprietary. These have not been formally standardized by letter designation or color code. Though not letter-designated, Seebeck properties of some commercial alloys that have significant use are addressed in ASTM Standard E1751 that presents NIST-defined Seebeck properties.
Most are relatively expensive high-temperature alloys that promise benefits of accuracy, stability, and environmental tolerance for special application. These include elemental pairs, Au vs. Pt, Pt vs. Pd, and Platinel®, a proprietary thermocouple alloy of Englehard Industries that has Seebeck characteristics very similar to Type K with improved stability and accuracy and with greater sensitivity than other precious metal materials.
The very pure precious metal thermocouples initially can be very accurate but are particularly vulnerable to contamination and introduced inhomogeneity in use. Infrequently, as usage broadens, additional commercially popular materials are considered for standardization. Producers and vendors apply proprietary trade names to letter-designated types.
A few apply their own unofficial letter designations and color codes. Informal designations might be inconsistent between sources. Identifiers assigned by individual manufacturers have no universal meaning. Letter Type U is ambiguous. German standard DIN EN 60584-1 specified thermocouple Type U as Cu vs. CuNi with brown jacket, red positive, Brown negative.
However, that letter also has ambiguously been used to denote a Cu/Cu pair used as a passive thermocouple extension or for RDT or thermistor wiring. Seebeck characteristics and informal color codes for nonstandardized materials should be confirmed by the vendor.
Unconventional Thermoelement Materials: Any thermoelectrically dissimilar pair of conducting materials can form a thermocouple. The absolute Seebeck characteristic of thermocouple platinum, Pt-67, a common thermoelectric reference material, was determined by the Center for Information and Numerical Data Analysis and Synthesis of Purdue University under contract to, but not published by, NIST. Others have published the E(T) absolute characteristic for platinum as well.
Limited information on Seebeck properties and application for a multitude of nonstandard materials used as thermoelements is available in papers or in one useful compendium. Most such combinations have not been used widely and are not appropriate for general thermometry.
Related Posts
- Thermocouple Working Principle
- Absolute Seebeck Effect
- Basic Thermocouple Circuits
- Extensions of Thermocouple
- Functional Model of Thermoelectric Circuits
- T/X Sketch of Dual-Reference Junction Circuit
- Applications of Functional Model
- Characteristics of Thermocouples
- Thermocouple Hardware
- Thermocouple Junction Styles
- Active Tests of Thermocouple
- Calibration of Thermocouples
- Thermocouple Thermometry Practice
- Distinctive Thermocouple Noise Problems