Hi friends,
In this article, I am going to discuss the synchronous motor working principle. I hope you will find it interesting and helpful.
Synchronous motor construction is very similar to that of a synchronous generator. Essential parts of the synchronous motor are the same as those of the synchronous generator i.e., a stator and a rotor.
The stator houses 3-phase armature winding in the slots of its laminated core, which are distributed over the entire yoke. This winding is similar to that used in synchronous generators and induction motors. It is connected to the 3-phase AC supply.
The field winding is placed in the rotor slots, and it is connected to the DC supply via two slip-rings. Due to this DC supply (known as excitation), rotor poles become N and S poles alternatively. The number of rotor poles is made equal to the number of stator poles. Modern synchronous motors often use brushless excitation. The rotor can be a salient-projected type or cylindrical type. Normally the salient pole rotor is preferred.
A simple synchronous motor is basically not self- starting. However, it can be made self-starting with the help of damper windings carried by the rotor poles. This motor is called synchronous motor because its rotor runs in synchronism with the synchronously rotating stator field.
Synchronous Motor Working Principle
The synchronous motor working principle is based on the principle of magnetic locking between stator and rotor poles.
To understand the working of synchronous motor, let the stator of the synchronous motor be wound for two poles. Let the rotor also produces two poles when they are excited by the external DC source.
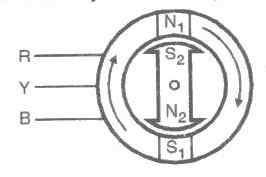
As the three-phase AC supply is connected to the stator winding, a rotating magnetic field (RMF) is produced. This field rotates at the synchronous speed Ns. The two poles produced are N1 and S1, as shown in the Figure.
These stator poles (N1 and S1) rotate in the air gap between stator and rotor at synchronous speed in the clockwise direction.
The rotor is then excited by the external DC source. It produces two poles N2 and S2, as shown in the Figure.
The rotor is accelerated, to rotate in the clockwise direction by some external engine. This is because the synchronous motor is not self-starting.
If unlike poles N1 – S2 and S1 – N2 come close to each other, then due to the strong force of attraction, magnetic locking takes place between them.
Once the stator and rotor poles are locked magnetically with each other, the rotor will continue to rotate at synchronous speed along with the rotating magnetic field. Then external engine coupled to the rotor can be decoupled.
The rotor will rotate at Ns as long as the magnetic lock between the stator and rotor continues to exist.
Synchronous Motor Working on Load
When a synchronous motor is connected to the lines and started by some external means, it starts rotating at synchronous speed. If the motor is running at no-load and has no losses, then induced EMF, E is equal and opposite to the applied voltage, and the stator and rotor poles are in line with each other, as shown in Figure.
The resultant EMF, Er, and hence the current drawn by the motor is zero. Thus the motor is said to be floating on the lines.
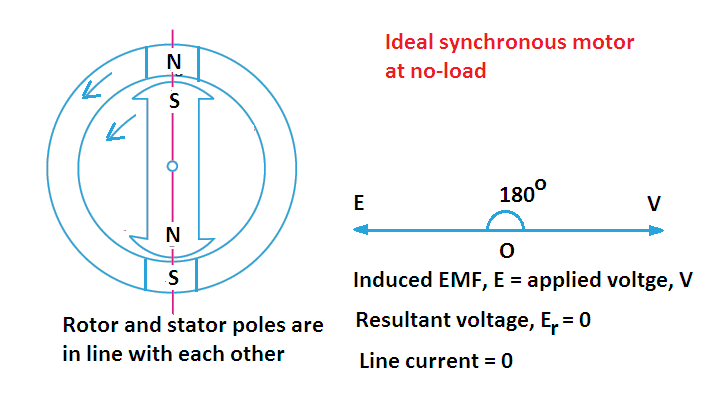
However, in an actual machine, some losses are always present with the result induced EMF; E falls back by a small angle, and the rotor poles also fall back by the same angle relative to the stator poles.
This causes a resultant voltage, Er across the armature and the motor draws no-load current from the mains. The power drawn by the motor is just sufficient to make the motor running continuously at the synchronous speed.
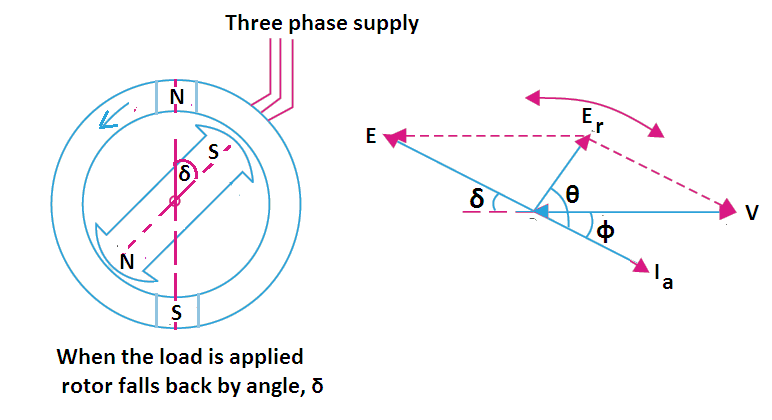
Now, when the load is applied to the shaft of the motor, the rotor falls back a little more relative to stator poles. Hence the torque angle or load angle, δ increases with the increase in load. This increases the resultant voltage, Er, which in turn increases the current drawn by the motor from mains.
Thus a synchronous motor is able to supply the increasing mechanical loads, not by the decrease in speed, but by shifting the position of rotor poles with respect to the stator poles.
When the load applied to the shaft of the motor is further increased, the rotor poles and induced EMF falls back further. Hence the load angle, δ, increases with the increase in the load. When δ increases, the resultant voltage Er increases, and so does the armature current.
If a too high mechanical load is applied to the synchronous motor, the rotor is pulled out of synchronism. And it comes to a standstill.
The maximum value of torque that a motor can develop without losing its synchronism is called pull-out torque.
Thanks for reading about “synchronous motor working principle” and “working principle of synchronous motor”. For more information, visit Wikipedia.