Calibration of Thermocouples
Thermocouple calibration is intended to improve accuracy. Conventional calibration might not. Calibration of a sample from a uniform set of as-delivered thermocouples to confirm conformity to standard tolerance is appropriate.
However, despite individual calibration, the approximated standard scaling relation, rather than the actual calibration, usually is used in thermometry regardless of calibration result. Individual calibration of each new thermocouple can reduce uncertainty only if the specific calibrations are used in data analysis.
Recalibration of thermocouples recognized or suspected as “drifting” in sensitivity is rarely beneficial. Some quality assurance programs mandate periodic recalibration of unused thermocouples.
Initial calibration applies generally so long as thermometry is restricted always to temperatures well below the upper temperature limit, in benign environments and for moderate duration. Sensitivity of unused thermocouples does not “age.”
Recalibration of severely used but possibly reusable thermocouples that have been suspected of error from observed drift is appropriate only after the subjects are proved acceptably homogeneous by authentic inhomogeneity test.
Otherwise, costly recalibration may be counterproductive in certifying a thermocouple that is not recognized to be seriously inhomogeneous by conventional calibration.
Option to Calibrate
Base-Metal Thermocouples: Two ways to address calibration problems presented by possible hidden inhomogeneity are the following: First, for inexpensive base-metal thermocouples, it is acceptable to presume that unused thermoelements are homogeneous within standardized tolerances.
First-cycle calibration of unused thermocouples with only brief exposure, and to temperatures, not exceeding a damage threshold, can usefully confirm the actual as-received state and allow more precise data analysis. Second, used base-metal wire thermocouples that have shown significant “drift” might be damaged only near the measuring junction. From the known circumstance of exposure, a length of segments believed damaged adjacent to the measuring junction could be discarded and the measuring junction re-formed. For relatively inexpensive thermocouples, economy may suggest that they be replaced if drift is suspected.
In-place recalibration of degraded thermocouples by comparison with reference thermocouple temporarily placed adjacent is often suggested. That common practice assumes the spurious junction-source model. Calibration is not of the “junction.” Such comparison presumes that the temperature distribution remains constant in thermometry.
However, the Functional Model clearly illustrates why in-place recalibration of a drifted inhomogeneous thermocouple can be deceptive if temperature distribution along the thermocouple varies in use.
Precious-Metal Thermocouples: The accuracy of precious-metal alloy thermocouples relies on their purity. They are vulnerable to contamination and inhomogeneity. Damage from the local migration, absorption, or evaporation of alloy constituents or other chemical contamination is not reversible.
However, unlike base-metal thermoelements, costly precious metal thermoelement materials sometimes can be reconditioned but only if they are degraded by plastic strain alone.
Platinum-based thermocouple wire might be annealed to an original state by electrically heating full length in air. Such annealed thermoelements can be presumed to be free only of reversible strain-induced inhomogeneity.
Confirming recalibration is justified after annealing, but homogeneity must be verified. Precious metal thermocouples have a significant material salvage value.
Calibration Process
Thermocouple calibration of effective E(T) requires immersing the thermoelements at the measuring junction into an isothermal calibration zone to a depth sufficient to assure that longitudinal heat conduction along the thermoelements does not affect the junction temperature.
A junction immersion depth of 10 – 20 times the thermocouple probe diameter is usually recommended. Emphasis on avoiding the effect of longitudinal heat conduction on measuring junction temperature is appropriate.
However, the spurious junction-source model has encouraged the false notion that it is the junction that is being calibrated. As illustrated by the Functional Model, the calibration emf is from unidentified segments of thermoelements, remote from the measuring junction where they pass through the temperature transition from calibration to room temperature.
Those unidentified segments then are presumed to be representative of the entire thermocouple. This conventional calibration obscures a practical fact. It is those thermoelement segments adjacent to the measuring junction that are most likely to become inhomogeneous in fabrication and application.
Significantly, it is those segments made isothermal that are the most likely to be inhomogeneous so they are eliminated from a recalibration.
Routine Calibration: Commercial bench top dry-block calibrators simplify routine calibration. Electronic refrigeration or heating applies the selected isothermal calibration temperature. Different units are required to cover a range from −30 °C to 1292 °C. Thermocouples are presumed to be homogeneous.
One or more probes of different diameters simultaneously can reside at sufficient depth in isothermal wells to assure that heat conduction along each probe does not affect measuring junction or reference temperature.
Certified Calibration: It is inefficient for incidental users of thermocouples to set up for formal thermocouple calibration. Calibration is often performed by specialized in-house or commercial calibration laboratories that offer calibration certified to be directly traceable to NIST.
In the most accurate calibration, fixed-point temperature cells realize intrinsic melting point temperatures of pure metals or the melting or triple point of water ice.
These sophisticated sources are more accurate and reproducible than dry-well calibrators or monitored baths. A set of cells, each of one particular metal and standardized freezing point temperature, imposes one of the few specific standardized temperatures. They are used in the establishment of the temperature scale, for thermocouple type-characterization, and in the most accurate calibration.
The sources are extremely accurate but are very costly and inconvenient to operate. They are used in the highest-level calibration and standards laboratories for calibration of homogeneous thermocouples. The melting point of pure water ice is most widely used to accurately impose the standard 0 °C reference temperature.
A Dewar thermal flask is filled with a slush of finely crushed ice just immersed in pure chilled de-ionized water. The flask is surrounded by crushed ice so the melting point temperature can be maintained for a very long duration. The flask must be deep enough to accommodate electrically insulated junctions to sufficient depth.
Such baths, properly established, can maintain the standard 0 °C melting point within 0.01 °C – 0.02 °C. Standard procedures for 0 °C reference baths are defined in ASTM standard E563-08.
A poorly formed and carelessly maintained bath of sizeable ice chunks in tap water in an un-insulated glass beaker might deviate from 0 °C by several degrees.
Calibration of Measuring-Junction
Thermocouple Assemblies Measuring junction thermocouple assemblies are of diverse specialized designs. The complicated geometry of some styles makes meaningful calibration difficult or impossible.
The Functional Model forces recognition that immersion of all or most of the thermocouple assembly into an isothermal oven actually eliminates it from the intended calibration.
Calibration of Reference-Junction
Thermocouple Assemblies Reference junction thermocouple assemblies are of the single-reference junction circuit style (Figure 1). The reference thermocouple is intended never to be exposed to either excessive temperature or to a degrading environment; therefore, its initial sensitivity is not expected to change.
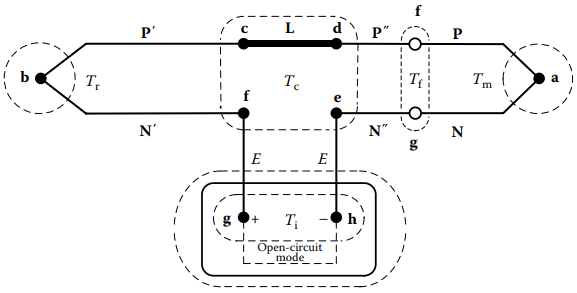
However, initial calibration should assure that the thermocouple is well within standard tolerance. Usually, they are not calibrated as sold and often not as used in calibration of measuring thermocouples.
Unfavorably, reference-junction-thermocouple assemblies always contribute some of the emf when used in a calibration procedure. With the measuring junction at ambient calibration temperature, all the emf is from the reference thermocouple; none from the test subject.
For calibration temperatures to about 40 °C, up to half the emf is from the reference thermocouple. It provides the portion of net emf from 0 °C to the ambient temperature at all higher calibration temperatures. If the reference is calibrated, the data cannot be used to correct calibrations of measuring junctions for which they were used.
Calibration of Monitor Scaling Functions
Usually, the scaling relations within monitors are not directly accessible to the user. Separate electronic calibrators for monitors allow scaling between emf and temperature to be confirmed. Scaling within the calibrator is performed by internal scaling relations that approximate with the standard tables. The user specifies a temperature and a thermocouple type.
The calibrator presents to the monitor a corresponding emf compensated for the temperature of its own reference terminals. The calibrator and monitor must be connected by an extension of the passive type. Such calibration is jointly of thermocouple and compensation scaling. Stand-alone reference temperature compensators can be calibrated by the same kind of electronic calibrator.
Calibration of Reference Temperature Compensators
Over the small span around normal ambient temperature, monitor reference temperature compensation uncertainties often range from 0.25 °C to 0.75 °C. Few monitors have reference temperature compensators that are separable for calibration.
Nevertheless, infrequently, both internal and external references have been observed to drift by many degrees. Such drift is usually unnoticed as it is indistinguishable from variation of measuring junction temperature.
Compensation should independently be confirmed. By temporarily shorting the input terminals, the monitor indicates the scaled temperature compensation it actually is applying. The monitor should indicate a plausible ambient temperature of the input terminals.
Related Posts
- Thermocouple Working Principle
- Absolute Seebeck Effect
- Basic Thermocouple Circuits
- Extensions of Thermocouple
- Functional Model of Thermoelectric Circuits
- T/X Sketch of Dual-Reference Junction Circuit
- Applications of Functional Model
- Characteristics of Thermocouples
- Thermocouple Hardware
- Thermocouple Junction Styles
- Active Tests of Thermocouple
- Calibration of Thermocouples
- Thermocouple Thermometry Practice
- Distinctive Thermocouple Noise Problems