A capacitor motor is also a split-phase induction motor. In this motor, starting winding has a capacitor in series with it. To start the motor, the necessary phase difference between both windings currents is produced by connecting a capacitor in series with it.
This is improved form of split phase motor. This type of motor was developed at the later stage. These motors have higher starting as well as running torque. This is the main advantage of capacitor motors over split-phase types.
The use of capacitor has many advantages.
1. The fluxes in the two windings, main winding as well as starting winding can be made to have a difference of 90o so that the motor becomes two phase motor.
Since the starting torque is proportional to the sine of the angle between the both winding currents, the starting torque is much higher than the usual split phase motor.
2. Starting line current reduced because of the capacitor connected in series with the starting winding.
3. The power factor of the motor gets improved. It can be made very near to unity in the capacitor motor where the capacitor is permanently fixed in the winding and it does not get disconnected.
There are two types of capacitor motors:
- Capacitor start motor.
- Capacitor Start-and-Run Motor
Capacitor Start Motor
In these motors, the necessary phase difference between Is and Im is produced by connecting a capacitor in series with the starting winding as shown in Fig. 36.10. The capacitor is generally of the electrolytic type and is usually mounted on the outside of the motor as a separate unit (Fig. 1).
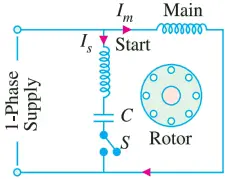
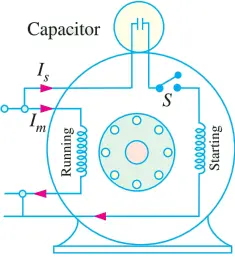
The capacitor is designed for extremely short-duty service and is guaranteed for not more than 20 periods of operation per hour, each period not to exceed 3 seconds.
When the motor reaches about 75 per cent of full speed, the centrifugal switch S opens and cuts out both the starting winding and the capacitor from the supply, thus leaving only the running winding across the lines.
As shown in Fig. 2, current Im drawn by the main winding lags the supply voltage V by a large angle whereas Is leads V by a certain angle. The two currents are out of phase with each other by about 80o (for a 200-W 50-Hz motor) as compared to nearly 30o for a split-phase motor.
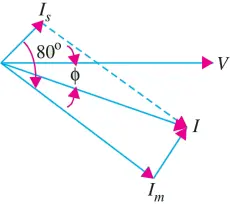
Their resultant current I is small and is almost in phase with V as shown in Fig. 3.
Since the torque developed by a split-phase motor is proportional to the sine of the angle between Is and Im, it is obvious that the increase in the angle (from 30o to 80o) alone increases the starting torque to nearly twice the value developed by a standard split-phase induction motor.
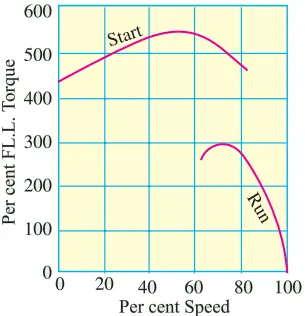
Other improvements in motor design have made it possible to increase the starting torque to a value as high as 350 to 450 percent. Typical performance curve of such a motor is shown in Fig. 4.
Capacitor Start-and-Run Motor
This motor is similar to the capacitor-start motor except that the starting winding and capacitor are connected in the circuit at all times. The advantages of leaving the capacitor permanently in circuit are
- improvement of over-load capacity of the motor
- a higher power factor
- higher efficiency and
- quieter running of the motor which is so much desirable for small power drives in offices and laboratories.
Some of these motors which start and run with one value of capacitance in the circuit are called single-value capacitor-run motors. Other which start with high value of capacitance but run with a low value of capacitance are known as two-value capacitor-run motors.
Single-value capacitor-Run Motor
It has one running winding and one starting winding in series with a capacitor as shown in Fig. 5. Since capacitor remains in the circuit permanently, this motor is often referred to as permanent split capacitor-run motor and behaves practically like an unbalanced 2-phase motor.
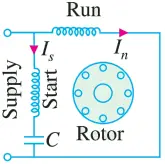
Obviously, there is no need to use a centrifugal switch which was necessary in the case of capacitor-start motors. Since the same capacitor is used for starting and running, it is obvious that neither optimum starting nor optimum running performance can be obtained because value of capacitance used must be a compromise between the best value for starting and that for running.
Generally, capacitors of 2 to 20 µF capacitance are employed and are more expensive oil or pyranol-insulated foil-paper capacitors because of continuous-duty rating.
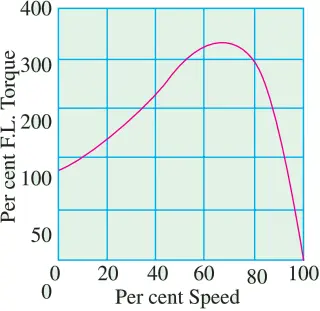
The low value of the capacitor results in small starting torque which is about 50 to 100 per cent of the rated torque (Fig. 6). Consequently, these motors are used where the required starting torque is low such as air-moving equipment i.e. fans, blowers and voltage regulators and also oil burners where quiet operation is particularly desirable.
One unique feature of this type of motor is that it can be easily reversed by an external switch provided its running and starting windings are identical. One serves as the running winding and the other as a starting winding for one direction of rotation.
For reverse rotation, the one that previously served as a running winding becomes the starting winding while the former starting winding serves as the running winding.
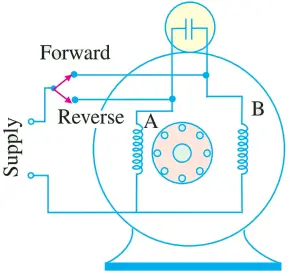
As seen from Fig. 7 when the switch is in the forward position, winding B serves as running winding and A as starting winding. When switch is in ‘reverse’ position, winding A becomes the running winding and B the starting winding.
Such reversible motors are often used for operating devices that must be moved back and forth very frequently such as rheostats, induction regulations, furnace controls, valves and arc-welding controls.
Two-value Capacitor-Run Motor
This motor starts with a high capacitor in series with the starting winding so that the starting torque is high. For running, a lower capacitor is substituted by the centrifugal switch. Both the running and starting windings remain in circuit. The two values of capacitance can be obtained as follows:
- by using two capacitors in parallel at the start and then switching out one for low-value run. (Fig. 8) or
- by using a step-up auto-transformer in conjunction with one capacitor so that effective capacitance value is increased for starting purposes.
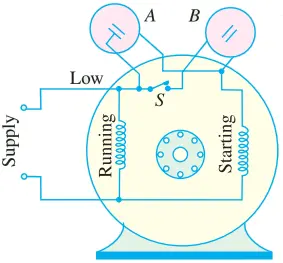
In Fig. 8, B is an electrolytic capacitor of high capacity (short duty) and A is an oil capacitor of low value (continuous duty). Generally, starting capacitor B is 10 to 15 times the running capacitor A.
At the start, when the centrifugal switch is closed, the two capacitors are put in parallel, so that their combined capacitance is the sum of their individual capacitances.
After the motor has reached 75 per cent full-load speed, the switch opens and only capacitor A remains in the starting winding circuit. In this way, both optimum starting and running performance is achieved in such motors.
If properly designed, such motors have operating characteristics very closely resembling those displayed by two-phase motors. Their performance is characterised by
- ability to start heavy loads
- extremely quiet operation
- higher efficiency and power factor
- ability to develop 25 per cent overload capacity
Hence, such motors are ideally suited where load requirements are severe as in the case of compressors and fire strokers etc. The use of an auto-transformer and single oil-type capacitor is illustrated in Fig. 9.
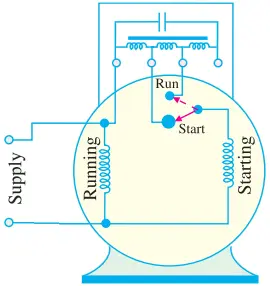
The transformer and capacitor are sealed in a rectangular iron box and mounted on top of the motor. The idea behind using this combination is that a capacitor of value C connected to the secondary of a step-up transformer, appears to the primary as though it had a value of K2C where K is voltage transformation ratio.
For example, if actual value of C = 4 µF and K = 6, then low-voltage primary acts as if it had a 144 µF ( = 62 × 4) capacitor connected across its terminals. Obviously, effective value of capacitance has increased 36 times.
In the ‘start’ position of the switch, the connection is made to the mid-tap of the auto-transformer so that K = 2. Hence, effective value of capacitance at start is 4 times the running value and is sufficient to give a high starting torque.
As the motor speeds up, the centrifugal switch shifts the capacitor from one voltage tap to another so that the voltage transformation ratio changes from higher value at starting to a lower value for running.