The biogas is produced by digestion, hydrolysis and hydro-gasification. The composition of biogas is as follows:
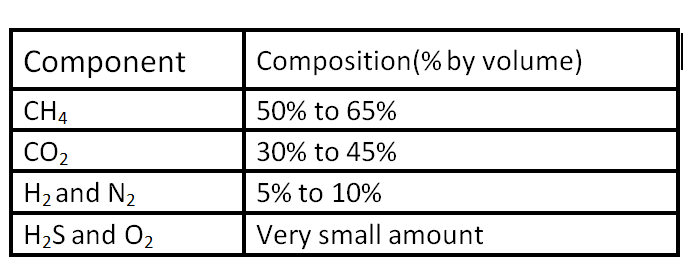
The presence of CO2, in biogas reduces its octane rating. The octane rating of biogas is 110 with CO2. In case the CO2 is removed from the biogas (CH4) its octane rating increases to about 130 as against the octane rating of petrol of 87.
The properties of biogas are as follows:
(i) It has excellent antiknock properties compared to petrol since it octane rating is higher than petrol.
(ii) Its auto-ignition temperature (730° C) is higher than petrol (470° C) which makes it a safer fuel. Therefore, it can use higher compression ratio.
(iii) It readily mixes with air even at low temperatures. Thus, it does not need to provide rich mixtures at the time of starting or at no loads (idling).
(iv) Only disadvantage using biogas is that it has low heating value compared to petrol. However, use of higher C.R. can compensate the loss of power output.
Application of Biogas in Petrol Engines
Biogas can be used in S.I. engines after initial starting the engine on petrol. It needs about 550 liters of gas per kWh to run a S.I. engine. The engine can either run purely on biogas. Also, it can run as dual-fuel engine either on biogas or petrol. It has the advantage that the engine can run on petrol if the availability of biogas is not there.
Minor modifications in the S.I. engine are needed like provision for supply of biogas, throttling of intake air and advancing the ignition timing.
Applications of Biogas in Diesel Engines
Biogas can be better used in C. I. engines in a duel fuel engine to improve its performance. It is more convenient to use biogas since it has high self ignition temperature of about 730° C. Moreover, the engine can be switched from duel fuel operation to diesel operation almost instantaneously in case of emergency.
In dual-fuel C.I. engine, the biogas is added to the air inducted into the engine. The mixture is compressed in the cylinder. Before, top dead centre (TDC), a small amount of diesel fuel called pilot fuel is injected through the conventional diesel fuel injection system.
This pilot fuel acts as the source of auto-ignition. The gas-air mixture in the vicinity of injected fuel spray ignites at number of places establishing the number of flame fronts. Now the combustion of fuel takes place by propagation of flame fronts as in S.I. engines.
The combustion process is rapid and smooth. The pilot-fuel injected required is about 7 to 8 percent of total heat of engine at full load. However, to run the engine at sufficient speed, the diesel fuel required to be injected is 15% to 20%.
The ignition injection timing for a normal diesel engine is 16° – 20° BTDC. The injection timing needs to be advanced slightly for its smooth and efficient functioning. It is necessary since retarding the engine causes the combustion to start only after TDC which in turn causes the reduction in power and efficiency.
Too much advancing the injection timing causes knocking of engine. Therefore, the modification of duel fuel engine using biogas (80%) and diesel fuel up to 20% as pilot fuel are:
(i) Advancing the injection timing of diesel fuel by 1° to 2°.
(ii) Provision of mixing chamber before air cleaner for through mixing of biogas and air before it is inducted into the cylinder during its suction stroke.
Advantages of Using Biogas In C.I. Engines
(i) A uniform gas-air mixture is available in multi-cylinder engines.
(ii) CO emissions are greatly reduced.
(iii) NOx emissions are almost 60% of diesel engines.
(iv) Formation of soot is almost eliminated.
(v) Pungent odor in exhaust is greatly reduced.
(vi) Clean combustion reduces the wear of engine parts and the lubricating oil consumption.
(vii) Only small amount of costly diesel fuel is needed to run the engine.
(viii) The heat of exhaust can be utilized for digesting the sludge in case of sewage disposal plants.
(ix) It has great flexibility of operation.
Other Applications of Biogas
- As fuel for cooking
- Power developed by engine using biogas can be used for lighting, pumping of water etc.
- As fuel for furnaces.
What is bio-fuel?
The conversion of certain biomass into alcohols and oils are called bio-fuels. These fuels have assumed significance because of their potential use in transport sector. These bio-fuels are being discussed below:
1. Methanol or Methyl Alcohol (CH3 OH) Methanol can be produced from fossil fuels like lignite or coal or from municipal solid wastes under extreme pressures and temperatures.
Though methanol engines give higher output and low emissions, but methanol cannot replace fully the gasoline in commercial vehicles due to its high boiling temperature and high latent heat of vaporization coupled with low vapor pressure.
It lowers the temperature of mixture in combustion chamber. It causes cold starting problems below 15°C temperature and makes an explosive mixture in the tank. It attacks rubber and plastic parts and causes corrosion and wear of the engine. However, blends of methanol with petrol up to 15% can be used. Blending of methanol with diesel is under active research.
2. Ethanol or Ethyl Alcohol (C2H5OH): The ethanol can be produced from sugar, starches (barley, wheat, corn, potatoes etc), and grains by fermentation. It can also be produced by cellulosic biomass by its hydrolysis to convert into sugar and then by fermentation. This production of ethanol from cellulosic process is quite complex. Ethanol can be blended with petrol up to 15% and it is a good alternate fuel for S.I. engines. It reduces emissions.
3. Bio-diesel: Bio-diesel is a methyl or ethyl ester of fatty acids made from vegetable oils and from animal fat. These fuels either in pure form or blended with diesel can be used in diesel engines with and without modification in the engine respectively.
Problem of using vegetable oils in pure form in diesel engines are caused by their high viscosity, fuel handling and pumping, atomization and fuel jet penetration. These oils have low volatility compared to diesel and produces higher carbon residue. These problems can be partially overcome by oil heating, esterification and thermal cracking of oil.
However blends of vegetable oils with diesel are called bio-diesel. Its use reduces emissions particularly the CO particulate matters but it causes slight increase in NOx emissions.
The edible oil like sun flower, peanut and soybean oils can be used as bio-diesel. Whereas the use of non-edible oils like jatropha and karanja oils is found to be very useful for diesel engine operations. Jatropha oil as bio-diesel is found to be very successful in C.I. engines.