The basic principle of resistance heating is that, when current passes through some resistance, power loss takes place which appears in the form of heat. There are two types of resistance heating, namely, direct resistance heating and indirect resistance heating.
Direct Resistance Heating
In the direct resistance heating, the electric current passes through the charge itself. This current produces I2R losses in the form of heat within the body itself. This principle is used in heating water by means of an electrode boiler.
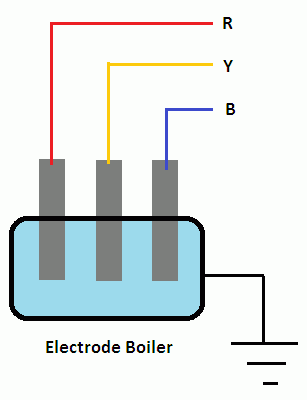
In the case of the electrode boiler, the electrodes are lowered into the tank filled with water. The current flow through electrodes into the water and water gets heated by I2R losses. For temperatures up to 100°C, mild steel electrodes are used.
The automatic stirring action is produced in the charge to be heated, and no external method of stirring is required to get uniform heating.
Indirect Resistance Heating
In the indirect resistance heating, the current does not flow through the body to be heated, but it flows through the resistance elements which get heated up. The heat is then transferred from the heating element to the charge mainly by radiation or convection.
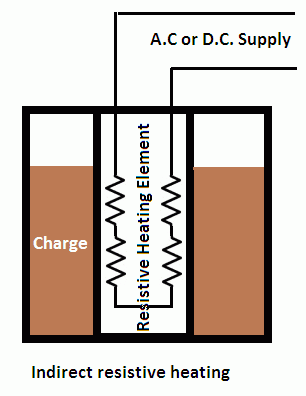
The figure shows a simple sketch of an indirect resistance heating oven. In this method, heat does not pass through the charge; hence natural stirring action is not there.
So some external stirring apparatus is employed to get uniform heating in indirect resistance heating method. The appliances that work on this principle include immersion rod, electric kettles, electric iron etc.
Temperature Control of Resistance Heating
Temperature control is necessary for resistance furnace or oven. The temperature may be kept constant or varied according to requirements. The control may be manual or automatic. The following ways can control the heat in an oven or furnace:
1. Use of variable Number of Elements: In this method, the number of heating elements in working is changed, so total power input is changed.
2. Change of Connections: In this method, connections of heating elements are changed by switches at different instants according to the requirements.
3. Transformer Tappings: We can control the voltage of the oven by using an autotransformer. It is an economical method of temperature control. Moreover, in this method, automatic temperature control can be obtained by thermostats.
4. SCRs can obtain very accurate heat control.
5. Thermostat control circuit: This is used in the automatic heating appliances to control the temperature. It is connected in series with the resistance element. It is made up of a bimetallic strip.
A bimetallic strip consists of two strips of different metals, having a different coefficient of expansions, securely fastened together. When the thermostat is connected in series with the resistance element current starts flowing through the thermostat, bimetallic strip starts bending.
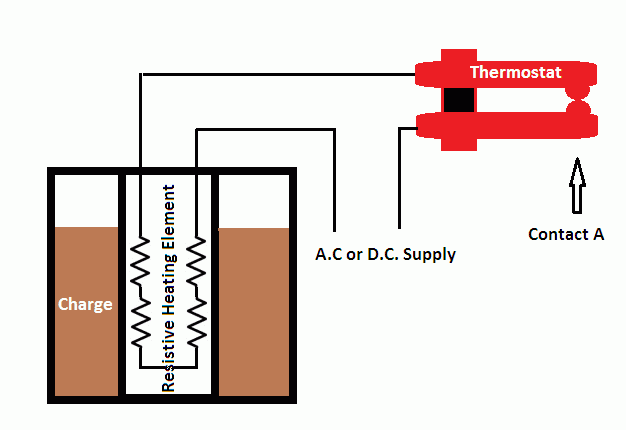
After some time contact point A shown in figure opens and the current flowing through the resistance element stops. Now no current is flowing through the circuit, bi-metallic strip starts cooling, bi-metallic strip regains its original shape and hence contact point A closes. Thus, thermostat controls heating of element by making and breaking the circuit again and again.
A screw is provided on the thermostat. It varies the tension between the two strips and hence alters the making and breaking time of the contact point A.
Properties of Resistance Heating Elements
High resistivity: It should have high specific resistance so that a small quantity of wire is required to produce a certain amount of heat.
The low-temperature coefficient of resistance: The resistance heating element material should possess the low-temperature coefficient of resistance, so that resistance may not vary with the change in temperature.
High melting point: The melting point of the material used should be very high so that high temperature can be obtained.
Free from oxidation: It should be free from oxidation to ensure a long life of the heating element.
The most common material used for the heating element is either alloy of nickel and chromium or the alloy of nickel, chromium and iron. These are used for temperatures up to 1100oC. The composition of the alloy for resistance heating elements depends upon the working temperature. For higher temperatures silicon carbide, tungsten and graphite are used.
Eureka is a copper-nickel alloy approximately 56% copper and 44% nickel. It is used where the low-temperature coefficient is required, such as in instrument coils, shunts, etc.
Thanks for reading about direct resistance heating and indirect resistance heating. For more information, visit wikipidia.