Dielectric heating is also known as radio frequency heating or electronic heating. When a non-metallic material such as wood, plastic, bone, or ceramic is subjected to an alternating electrostatic field, the dielectric loss occurs in it. This loss appears in the form of heat in dielectric heating. It is the basic dielectric heating principle.
A dielectric material has positively and negatively charged ions. If we place such material between two electrodes and charge them positive and negative, respectively, the molecules will tend to line up all in one direction (see Figure 1).
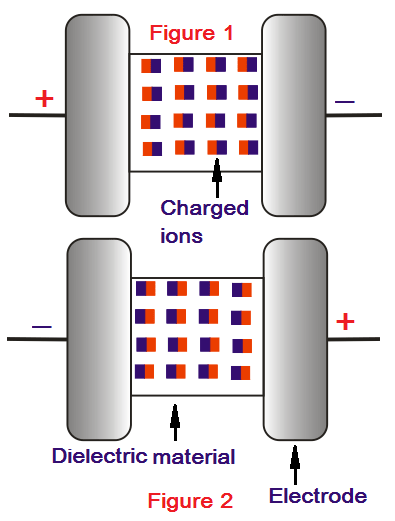
If we reverse the charge on the electrodes, they will tend to flip around and line up in the opposite direction (see Figure 2). Reversing the charge causes the molecules to rub against one another. This process produces ‘frictional’ heating in the material. The rate of heating will increase as the frequency of reversal is increased.
The same phenomenon takes place in a material during the dielectric heating. When we apply a high-frequency voltage across a material during the dielectric heating, its molecules line up again and again. In doing so, they rub against one another and produces frictional heating. As the frequency of reversal of the field (i.e., supply frequency) is very high, a large amount of heat is produced.
Dielectric Heating Set Up
In this process, the material to be heated is placed as a slab between two metallic electrodes across which high-frequency voltage is applied. The applied voltage varies from 10 to 20 kV.
To ensure sufficient loss and to give an adequate amount of heating, frequencies between 10 to 20 MHz must be used. At higher frequencies, we can obtain better heating efficiencies and better coupling. So the higher frequencies are very suitable for low volume products and low coupling materials. The necessary high-frequency supply voltage is obtained from a valve oscillator.
The whole setup of the dielectric heating is equivalent to a capacitor. Here, material to be heated is just equal to the dielectric material of the capacitor.
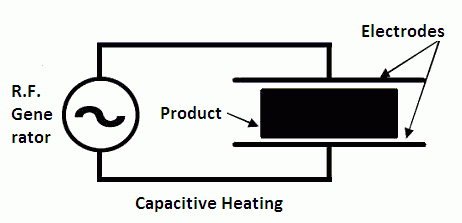
The current drawn by the capacitor, when an A.C. supply voltage is applied across its two plates, does not lead the supply voltage by 90° exactly. It means that there is a particular component of the current which is in phase with the voltage. This component of the current produces heat in dielectric material placed in between the two plates of the capacitor.
This electric energy, dissipated in the form of heat energy in the dielectric material, is known as the dielectric loss. The dielectric loss is directly proportional to V 2f. That is why we use a high-frequency voltage in dielectric heating.
Temperature Profile For Dielectric heating
In the dielectric heating process, the high-frequency waves heat the material in the complete volume by penetrating the material, depending on the penetration depth of the waves. Provided the material is not too thick; the high-frequency waves transfer almost the same amount of energy to every volume element of the material. It results in a homogeneous temperature increase in the material.
Theoretically, this would provide the same temperature to every volume element. In a practical situation, the surface of the material would lose heat to the ambient atmosphere, which is not heated by the high-frequency waves. Therefore the surface temperature is reduced. So the highest temperature is on the inside, whereas the lowest temperature is on the surface of the material. So this temperature profile is inverse to one of the conventional heating processes (see Figure 4).
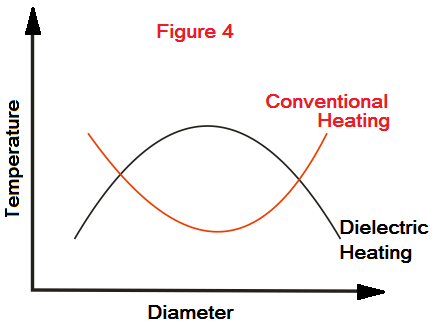
In this process, heating is very much dependent on the dielectric properties of the material, and they depend on the frequency and temperature.
The dielectric properties of some materials are mainly dependent on temperature, whereby the coupling is increased as the temperature increases. These materials are prone to a thermal runaway effect that is initially caused by low-temperature differences in the material.
This effect results in a faster temperature increase, which in turn leads to even better coupling and increased energy take-up, and so on. This thermal runaway can result in local destruction or even melting of the material.
Advantages of Dielectric Heating
1. Since the heat is produced throughout the whole mass of material, we get uniform heating. By the conventional methods of heating, it is not possible.
2. A shorter time is required to complete the process as compared to other methods.
3. It is suitable for non-conducting materials like wood, plastics, and synthetic compounds, etc.
Disadvantages of Dielectric Heating
1. Since heat produced in dielectric heating very much depends upon the type of material, the product size, the power density, etc., so we can heat only those materials which have a high dielectric loss. It is not possible to heat a transparent or reflective material by this method.
2. The cost of equipment required for dielectric heating is so high that we use this method only where other methods are impracticable or too slow.
3. The overall efficiency of dielectric heating is very low (about 50%).
4. High frequencies may cause radio interference.
Applications of Dielectric Heating
1. It is used for drying of textiles, manufacture of plywood, paper, etc. The overall efficiency in this case of dielectric heating is about 50%.
2. It is used also employed in drying tobacco, paper, wood, gluing, and bonding of woods.
3. It is used to weld the PVC.
4. It is used in producing artificial fibers, heating of bones and tissues, etc.
5. It is used in food processing.
6. In high-temperature dielectric heating applications, we can combine it with other conventional heating methods like resistance heating or hot air heating.
This combination can reduce some of the difficulties of pure dielectric heating, i.e., a strong influence of the product material on the heating, requirement of susceptor pre-heating, and so on. Especially for large volume batch furnaces and continuous furnaces, the hybrid concept may be very beneficial.
Thanks for reading about the “dielectric heating working principle.”