Mechanical Pressure Sensing Elements
Mechanical pressure-sensing elements include the bellows, the diaphragm, and the bourdon tube. Each of these devices converts a fluid pressure into a force.
If unrestrained, the natural elastic properties of the element will produce a motion proportional to the applied pressure.
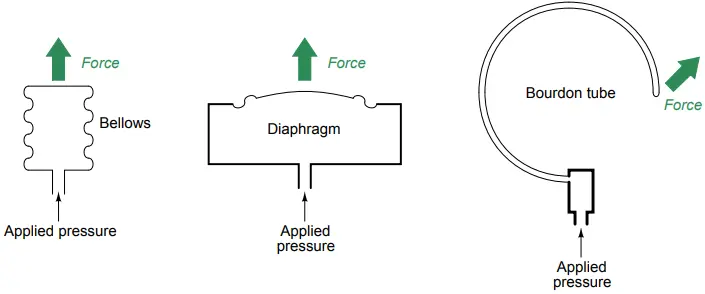
Bellows resemble an accordion constructed from metal instead of fabric. Increasing pressure inside a bellows unit causes it to elongate.
A diaphragm is nothing more than a thin disk of material which bows outward under the influence of a fluid pressure. Many diaphragms are constructed from metal, which gives them spring-like qualities.
Some diaphragms are intentionally constructed out of materials with little strength, such that there is negligible spring effect. These are called slack diaphragms, and they are used in conjunction with external mechanisms (e.g. springs) producing the necessary restraining force to prevent damage from applied pressure.
The following photograph shows the mechanism of a small pressure gauge using a brass diaphragm as the sensing element.
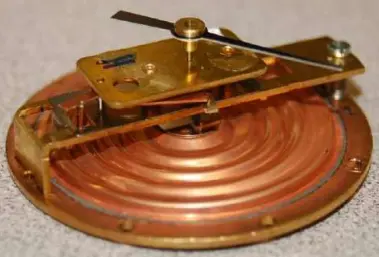
As pressure is applied to the rear of the diaphragm, it distends upward (away from the table on which it rests as shown in the photograph), causing a small shaft to twist in response.
This twisting motion is transferred to a lever which pulls on a tiny link chain wrapped around the pointer shaft, causing it to rotate and move the pointer needle around the gauge scale. Both the needle and scale on this gauge mechanism have been removed for easier viewing of diaphragm and mechanism.
Bourdon tubes are made of spring-like metal alloys bent into a circular shape. Under the influence of internal pressure, a bourdon tube “tries” to straighten out into its original shape before being bent at the time of manufacture.
Most pressure gauges use a bourdon tube as their pressure-sensing element. Most pressure transmitters use a diaphragm as their pressure-sensing element.
Bourdon tubes may be made in spiral or helical forms for greater motion (and therefore greater gauge resolution). The Bourdon tube pressure element is a very robust and time-tested design.
A photograph of a C-tube pressure gauge mechanism (taken from the rear of the gauge, behind the pointer and scale) reveals its mechanical workings.
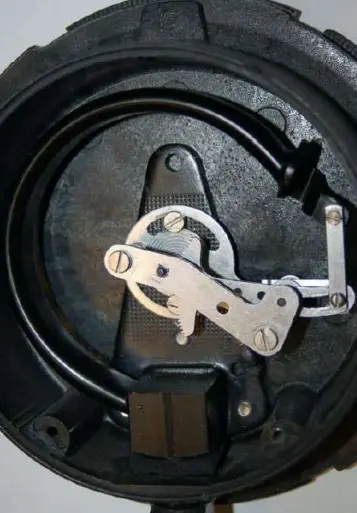
The dark, C-shaped tube is the bourdon tube sensing element, while the shiny metal parts are the linkage, lever, and gear assembly.
The next photograph shows a spiral bourdon tube, designed to produce a wider range of motion than a C-tube bourdon.
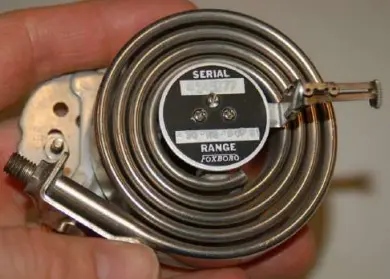
It should be noted that bellows, diaphragms, and bourdon tubes alike may all be used to measure differential and/or absolute pressure in addition to gauge pressure.
All that is needed for these other functionalities is to subject the other side of each pressure-sensing element to either another applied pressure (in the case of differential measurement) or to a vacuum chamber (in the case of absolute pressure measurement).
This next set of illustrations shows how bellows, diaphragms, and bourdon tubes may be used as differential pressure-sensing elements.
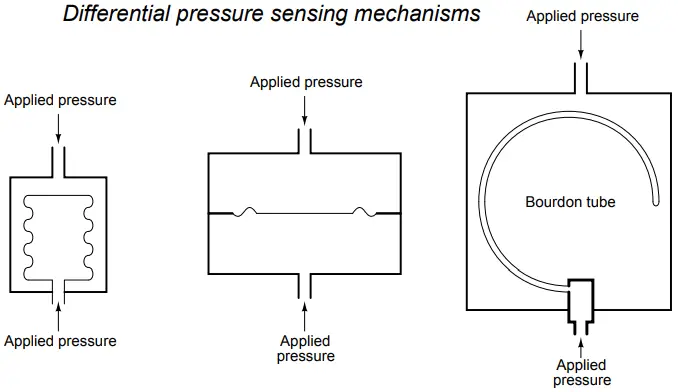
The challenge in doing this, of course, is how to extract the mechanical motion of the pressuresensing element to an external mechanism (such as a pointer) while maintaining a good pressure seal.
In gauge pressure mechanisms, this is no problem because one side of the pressure-sensing element must be exposed to atmospheric pressure anyway, and so that side is always available for mechanical connection.
A differential pressure gauge is shown in the next photograph. The two pressure ports are clearly evident on either side of the gauge.
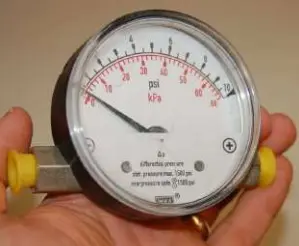
Mechanical Adaptations
Most modern electronic pressure sensors convert very small diaphragm motions into electrical signals through the use of sensitive motion-sensing techniques (strain gauge sensors, differential capacitance cells, etc.).
Diaphragms made from elastic materials behave as springs, but circular diaphragms exhibit very nonlinear behavior when significantly stretched unlike classic spring designs such as coil and leaf springs which exhibit linear behavior over a wide range of motion.
Therefore, in order to yield a linear response to pressure, a diaphragm-based pressure sensor must be designed in such a way that the diaphragm stretches very little over the normal range of operation.
Limiting the displacement of a diaphragm necessitates highly sensitive motion-detection techniques such as strain gauge sensors, differential capacitance cells, and mechanical resonance sensors to convert that diaphragm’s very slight motion into an electronic signal.
An alternative approach to electronic pressure measurement is to use mechanical pressuresensing elements with more linear pressure-displacement characteristics – such as bourdon tubes and spring-loaded bellows – and then detect the large-scale motion of the pressure element using a less-sophisticated electrical motion-sensing device such as a potentiometer, LVDT, or Hall Effect sensor.
In other words, we take the sort of mechanism commonly found in a direct-reading pressure gauge and attach it to a potentiometer (or similar device) to derive an electrical signal from the pressure measurement.
This alternative approach is undeniably simpler and less expensive to manufacture than the more sophisticated approaches used with diaphragm-based pressure instruments, but is prone to greater inaccuracies.
Even bourdon tubes and bellows are not perfectly linear spring elements, and the substantial motions involved with using such pressure elements introduces the possibility of hysteresis errors due to mechanism friction, and deadband errors due to backlash (looseness) in mechanical connections. You are likely to encounter this sort of pressure instrument design in direct-reading gauges equipped with electronic transmitting capability.
An instrument manufacturer will take a proven product line of pressure gauge and add a motion-sensing device to it that generates an electric signal proportional to mechanical movement inside the gauge, resulting in an inexpensive pressure transmitter that happens to double as a direct-reading pressure gauge.