Different Types of Process Control Switches
There are different types of process control switches. These are:
- Limit switch
- Proximity switch
- Pressure switch
- Level switch
- Temperature switch
- Flow switch
Limit Switch
A limit switch detects the physical motion of an object by direct contact with that object.
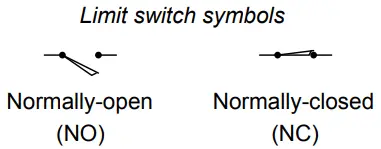
An example of a limit switch is the switch detecting the open position of an automobile door, automatically energizing the cabin light when the door opens.
A limit switch will be in its “normal” status when it is not in contact with anything (i.e. nothing touching the switch actuator mechanism).
Limit switches find many uses in industry, particular in robotic control and CNC (Computer Numerical Control) machine tool systems. In many motion-control systems, the moving elements have “home” positions where the computer assigns a position value of zero.
For example, the axis controls on a CNC machine tool such as a lathe or mill all return to their “home” positions upon start-up, so the computer can know with confidence the starting locations of each piece. These home positions are detected by means of limit switches.
The computer commands each servo motor to travel fully in one direction until a limit switch on each axis trips. The position counter for each axis resets to zero as soon as the respective limit switch detects that the home position has been reached.
A typical limit switch design uses a roller-tipped lever to make contact with the moving part.
Screw terminals on the switch body provide connection points with the NC and NO contacts inside the switch. Most limit switches of this design share a “common” terminal between the NC and NO contacts like this:
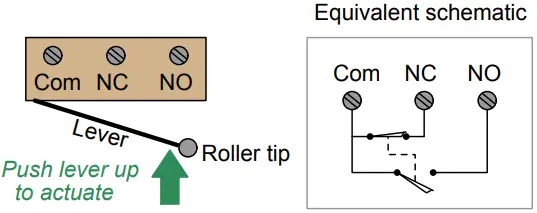
This switch contact arrangement is sometimes referred to as a form-C contact set, since it incorporates both a form-A contact (normally-open) as well as a form-B contact (normally-closed).
Proximity Switches
A proximity switch is one detecting the proximity (closeness) of some object. By definition, these switches are non-contact sensors, using magnetic, electric, or optical means to sense the proximity of objects.
A proximity switch will be in its “normal” status when it is distant from any detectable object.
Being non-contact in nature, proximity switches are often used instead of direct-contact limit switches for the same purpose of detecting the position of a machine part, with the advantage of never wearing out over time due to repeated physical contact.
Most proximity switches are active in design. That is, they incorporate a powered electronic circuit to sense the proximity of an object.
- Inductive proximity switches sense the presence of metallic objects through the use of a high-frequency magnetic field.
- Capacitive proximity switches sense the presence of non-metallic objects through the use of a high-frequency electric field.
- Optical proximity switches detect the interruption of a light beam by an object.
- Ultrasonic proximity switches sense the presence of dense matter by the reflection of sound waves.
The schematic diagram symbol for a proximity switch with mechanical contacts is the same as for a mechanical limit switch, except the switch symbol is enclosed by a diamond shape, indicating a powered (active) device:
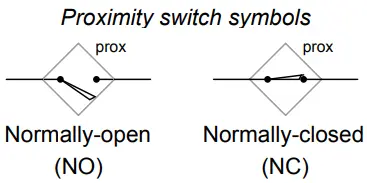
Usually output elements of proximity switches are transistors configured either to source current or sink current. The terms “sourcing” and “sinking” are best understood by visualizing electric current in the direction of conventional flow rather than electron flow.
The following schematic diagrams contrast the two modes of switch operation, using red arrows to show the direction of current (conventional flow notation). In both examples, the load being driven by each proximity switch is a light-emitting diode (LED):
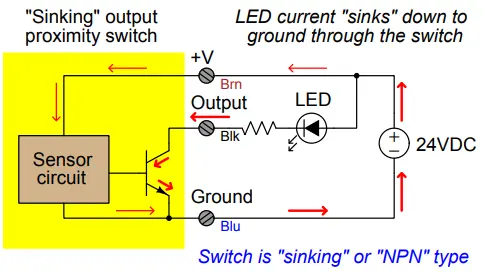
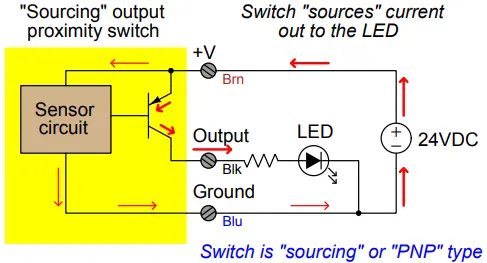
A common coloring convention for electronic proximity switches is brown for +V power supply, blue for ground (− pole of power supply), and black for the switched output signal. This convention is common to sinking and sourcing proximity switches alike.
An electronic switch designed to sink current through its signal wire is alternatively referred to as an NPN switch due to the type of transistor used in its output.
Conversely, an electronic switch designed to source current through its signal wire may be referred to as a PNP switch.
The key to understanding these labels is to recognize the emitter terminal of the output transistor is always the one connected to the power supply rail.
For a sinking switch, this means the emitter must connect to the negative rail, necessitating an NPN transistor to do the switching.
For a sourcing switch, this means the emitter must connect to the positive rail, in which case only a PNP transistor will suffice.
Yet another convention for describing sourcing and sinking transistor switches is to refer to them as high-side switches and low-side switches, respectively.
A sourcing transistor (PNP) has its emitter terminal attached directly to the “high” rail (+) of the DC power supply.
A sinking transistor (NPN), by contrast, has its emitter terminal attached directly to the “low” rail (−) of the DC power supply.
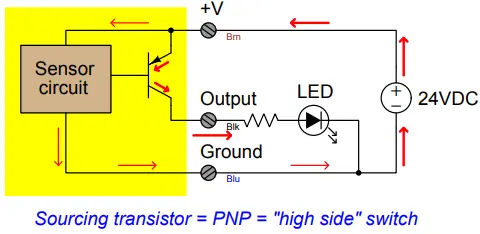
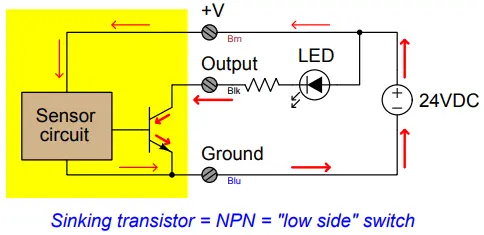
Many industrial proximity switches have built-in LED indicator lamps to help technicians diagnose circuit problems by directly indicating switch status. With just a glance, one may tell whether or not the proximity switch is detecting the presence of an object.
Like other types of process switches, proximity switches come in both “normally open” (NO) and “normally closed” (NC) varieties. This distinction has nothing whatsoever to do with sourcing versus sinking (PNP vs. NPN), but rather what the status of the proximity switch will be when no objects are near.
These switch characteristics are commonly fixed, and must be specified when ordering the device.
Likewise, the detection range of a proximity switch is usually a fixed parameter rather than being adjustable.
Pressure Switches
A pressure switch is one detecting the presence of fluid pressure. Pressure switches often use diaphragms or bellows as the pressure-sensing element, the motion of which actuates one or more switch contacts.
A pressure switch will be in its “normal” status when it senses minimum pressure. For a pressure switch, “normal” status is any fluid pressure below the trip threshold of the switch.
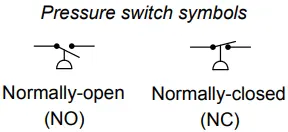
A legacy design of pressure switch uses a bourdon tube as the pressure-sensing element, and a glass bulb partially filled with mercury as the electrical switching element.
When applied pressure causes the bourdon tube to flex sufficiently, the glass bulb tilts far enough to cause the mercury to fall against a pair of electrodes, thus completing an electrical circuit.
Advantages of mercury tilt switches include immunity to switch contact degradation from harmful atmospheres (oil mist, dirt, dust, corrosion) as well as safety in explosive atmospheres (since a spark contained within a hermetically sealed glass bulb cannot touch off an explosion in the surrounding atmosphere).
Disadvantages include the possibility of intermittent electrical contact resulting from mechanical vibration, as well as sensitivity to mounting angle.
Level Switches
A level switch is one detecting the level of liquid or solid (granules or powder) in a vessel. Level switches often use floats as the level-sensing element, the motion of which actuates one or more switch contacts.
A level switch will be in its “normal” status when it senses minimum level (e.g. an empty vessel). For a level switch, “normal” status is any fluid level below the trip threshold of the switch.
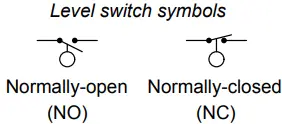
Float-type Level Switches: Some level switches use a float to sense the level of a liquid surface, actuating an electrical switch by the motion of the float. The electrical schematic symbol for a level switch is actually based on this type of mechanism, with a round “ball” float drawn as the actuating element.
There are many simple float switch designs for direct installation in open (vented) process vessels, resembling the float valve assembly on a water-flush toilet.
Any “limit” style switching element will work here, including inductive proximity switches, to sense the float’s position in an environment where no isolation need exist between the switch and the process fluid(s).
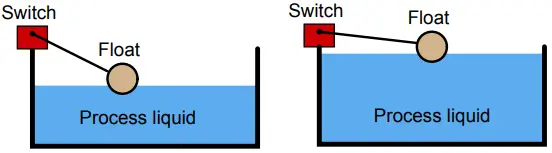
Tuning Fork Level Switches: This level switch uses a metal tuning fork structure to detect the presence of a liquid or solid (powder or granules) in a vessel. An electronic circuit continuously excites the tuning fork, causing it to mechanically vibrate.
When the prongs of the fork contact anything with substantial mass, the resonant frequency of the fork decreases. The circuit detects this frequency change and indicates the presence of mass contacting the fork.
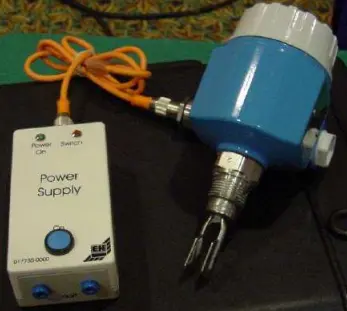
The forks’ vibrating motion tends to shake off any accumulated material, such that this style of level switch tends to be resistant to fouling.
It should be noted that the previous photograph of the tuning-fork style level switch is complete: the fork “paddles” are only a couple of inches long and require no physical extensions in order to properly detect liquid or solid material at that point.
Paddle-wheel Level Switches: A more primitive variation on the theme of a “tuning fork” level switch is the rotating paddle switch, used to detect the level of powder or granular solid material. This level switch uses an electric motor to slowly rotate a metal paddle inside the process vessel.
If solid material rises to the level of the paddle, the material’s bulk will place a mechanical load on the paddle. A torque-sensitive switch mechanically linked to the motor actuates when enough torsional effort is detected on the part of the motor.
A great many level switches of this design sold in the United States under the trade-name Bindicator (so-called because they detected the level of solid material in storage bins).
Ultrasonic Level Switches: Yet another style of electronic level switch uses ultrasonic sound waves to detect the presence of process material (either solid or liquid) at one point.
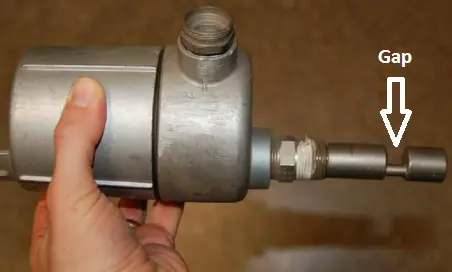
Sound waves pass back and forth within the gap of the probe, sent and received by piezoelectric transducers. The presence of any substance other than gas within that gap affects the received audio power, thus signaling to the electronic circuit within the bulkier portion of the device that process level has reached the detection point.
The lack of moving parts makes this probe quite reliable, although it may become “fooled” by heavy fouling.
Capacitive Level Switches: Another electronic liquid level switch technology is capacitive: sensing level by changes in electrical capacitance between the switch and the liquid.
Conductive Level Switches: Perhaps the simplest (and oldest) form of electrical level detection is where a pair of metal electrodes contacts the process material to form a complete electrical circuit, actuating a relay. This type of switch, of course, only works with granular solids and liquids that are electrically conductive (e.g. potable or dirty water, acids, caustics, food liquids, coal, metal powders) and not with nonconducting materials (e.g. ultra-pure water, oils, ceramic powders).
A legacy design for conductive level switches is the model 1500 “induction relay” originally manufactured by B/W Controls, using a special transformer/relay to generate an isolated AC probe voltage and sense the presence of liquid.

Line voltage (120 VAC) energizes the primary coil, sending a magnetic field through the laminated ferrous core of the relay. This magnetic field easily passes through the center of the secondary coil when the secondary circuit is open (no liquid closing the probe circuit), thus completing the magnetic “circuit” in the core. With the magnetic circuit thus completed, the armature will not be attracted to the core.
However, when a circuit is completed by liquid level rising to contact both probes, the secondary coil’s resulting current “bucks” the magnetic flux through its center, causing more magnetic flux to bypass to the end poles where it attracts the ferrous armature toward the core frame.
This physical attraction actuates switch contacts which then signal the presence of liquid level at the probes.
The following pair of illustrations shows the two conditions of this level switch, with the magnetic lines of flux highlighted as dashed lines through the core.
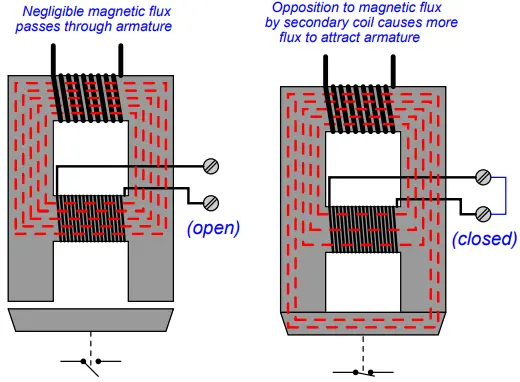
The “transformer” design of this particular conductive level switch not only provides electrical isolation between the probes and the energizing (120 VAC) circuit, but it also enables a wide range of detection voltages to be generated for the probes just by altering the number of wire “turns” in the secondary coil.
The B/W Controls model 1500 inductive relay is available in a variety of AC voltage output levels, ranging from 12 VAC (for detecting metallic substances) to 800 VAC for use with demineralized water such as that found in steam boiler systems.
More modern variations on the same design theme use much lower AC voltages to energize the probes, employing sensitive semiconductor amplifier circuits to detect probe current and signal liquid level.
Temperature Switches
A temperature switch is one detecting the temperature of some substance. Temperature switches often use bimetallic strips as the temperature-sensing element, the motion of which actuates one or more switch contacts.
An alternative design uses a metal bulb filled with a fluid that expands
with temperature, causing the switch mechanism to actuate based on the pressure this fluid exerts against a diaphragm or bellows.
This latter temperature switch design is really a pressure switch, whose pressure is a direct function of process temperature by virtue of the physics of the entrapped fluid inside the sensing bulb.
A temperature switch will be in its “normal” status when it senses minimum temperature (i.e. cold, in some cases a condition colder than ambient). For a temperature switch, “normal” status is any sensed temperature below the trip threshold of the switch.
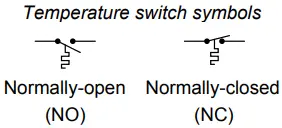
Like all other process switches, temperature switches exhibit a certain amount of deadband in their switching action. A temperature switch that trips at 300 oF rising, for example, will not re-set at 300 oF falling. That switch would more likely reset at some lower temperature such as 295 oF.
With mechanical switch designs, some amount of deadband is inevitable due to friction inside the mechanism. However, process switch deadband is actually a useful characteristic as it helps avoid repeated “nuisance” alarms from happening.
Some mechanical temperature switches come equipped with a separate adjustment for deadband (also called differential). Setting this deadband adjustment in a mechanical temperature switch requires the technician to repeatedly subject the sensing element to a rising and falling temperature, to check that the switch trips at the proper setting and resets at the proper setting.
For discrete temperature-sensing applications demanding high accuracy and repeatability, electronic temperature switch circuits using thermocouples, RTDs, or thermistors may be used instead of a mechanical (bi-metallic or filled bulb) sensing element.
With electronic temperature switches, the adjustment of deadband (differential) is both precise and flexible. Unlike mechanical switches where deadband is primarily a function of friction, and therefore liable to change over time as the device wears, electronic switching circuits may be precisely set for any trip and reset points along its measurement range, remaining very stable over time.
Flow Switches
A flow switch is one detecting the flow of some fluid through a pipe. Flow switches often use “paddles” as the flow-sensing element, the motion of which actuates one or more switch contacts.
A flow switch will be in its “normal” status when it senses minimum flow (i.e. no fluid moving through the pipe). For a flow switch, “normal” status is any fluid flow rate below the trip threshold of the switch.
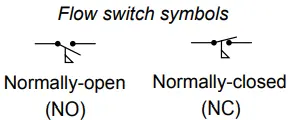
A simple paddle placed in the midst of a fluid stream generates a mechanical force which may be used to actuate a switch mechanism. Like all other process switches, flow switches exhibit deadband (also called differential) in their switching action.
A flow switch that trips at 15 GPM rising, for example, will not re-set at 15 GPM falling. That switch would more likely reset at some lower flow rate such as 14 GPM. With the “trip” and “reset” points being different, the switch avoids unnecessary cycling if the process flow rate hovers near one critical value.