Overheating is a major cause of insulation and bearing failure. 3 phase motor overheating reasons are as under:
Line-Caused Motor Overheating Reasons
There are four causes of line-caused overheating: overvoltage, low voltage, unbalanced voltage, and a high-resistance connection.
Overvoltage: Overvoltage can cause a normally loaded motor to overheat. NEMA standard specifications allow motors a voltage deviation of ± 10 percent from their nameplate voltage rating. All motors will start their load faster when voltage is high.
Low Voltage: Low voltage affects all motors in the same way—they lose power and may take too long to start a load. Prolonged starts cause excess heat in the stator winding (at the start of its duty cycle).
Another concern with low voltage is the heat that develops from frequent starting. Under maximum load, low voltage causes the motor to run more slowly than the nameplate RPM. Technically, it’s overloaded. It will run hot and will soon fail.
If the service wire to a motor is too small, it causes low voltage (especially when starting). Some symptoms are frequently blown fuses or tripped protection devices. Voltage normally drops briefly from the motor’s high starting current, but the voltage should come back up to nearly its full value as soon the motor reaches full speed.
High-efficiency motors draw higher starting current than standard motors. This may require an increase in the wire size of the feeder line.
Motors with a maximum load are the first to react to low voltage. A prime example was a motor that tripped its overload protector at a certain time of the day. The cause was traced to a high-ampere load coming online (elsewhere in the plant) at that time, lowering the voltage for the entire plant. Power lines that are loaded nearly to their capacity can have intermittent low voltage. A brief high-load demand from another location will cause a voltage drop.
Power companies put capacitors across the lines to correct the low power factor. Low voltage will develop if the capacitors fail.
A voltage recorder should be used if incoming power problems are suspected. The recorder should be on long enough to include every load variation the location has.
Unbalanced Voltage: Unbalanced voltage has many sources:
- Failed power-factor-correcting capacitors can affect the voltage of an entire building.
- A high-resistance connection is a frequent cause of an unbalance. This problem can be easily spotted with infrared instruments.
- Unbalanced single-phase loading (such as lighting and single-phase motors) is a frequent cause of unbalanced voltage. Lighting load can be balanced at the distribution panel. (A single-phase air conditioner is an example of a motor load that is hard to balance, due to the air conditioner’s intermittent operation.)
- Another cause of unbalanced voltage-related heating is worn contacts (in a motor starter) that don’t make a solid connection.
- Unbalanced voltage will cause a motor to overheat even if it is lightly loaded.
High-Resistance Connection: A high-resistance connection is one of the more frequent causes of electric motor failure. Because of a motor’s high starting current, its ampere load is very different from most electrical loads.
Every connection in the motor’s supply circuit is subjected to a brief high-ampere stress when it starts. These connections should be checked regularly (more often if the motor starts frequently).
Increasing the supply line wire size (one size above the code requirement) is a one-time cost that decreases the chance of motor failure.
The connecting terminals in a disconnect switch and/or a motor control are common spots for high-resistance connections.
Disconnect and control connections should be routinely checked and tightened. A small infrared gun can be used to check connections. All connections should be at the same temperature.
Aluminum wire has a notorious reputation for developing loose connections. Its use is not recommended for an electric motor load.
Motor lead lugs should be thick enough (throughout the connection) to represent the circular mil area (size) of the motor’s lead wire. If any part of the lug is too small, it becomes a resistor in series with the motor, and current will be restricted when the motor needs it the most—to start the load.
Operator-Caused Motor Overheating Reasons
Operators often cause motors to overheat. If paid by the unit, operators often overload the machine. The mining industry is a case in point. An overloaded induction motor can be quickty checked with a tachometer. Compare the tachometer reading with the motor’s nameplate.
Just a few RPM slower than the nameplate RPM will cause overheating. The design A (or a high-efficiency) motor will run hotter than a standard induction motor under this condition. This can be seen in the torque curve that the design A motor develops near its full-load speed (Figure 1).
Frequent starting and stopping often causes excessive heating in motors above 25 horsepower. The physical mass of a large motor doesn’t dissipate heat easily. Most motors will cool better while running with no load than when shut off. If a motor is required to start often, forced ventilation or the use of a clutch should be considered if motor failure is frequent.
An abrupt speed change is harmful to all motors, but especially to brush-type (DC and wound-rotor three-phase) motors. The design D induction motor should be considered if its torque curve is compatible with the load requirement.
Just a few RPM slower than the nameplate RPM will cause overheating. The design A (or a high-efficiency) motor will run hotter than a standard induction motor under this condition. This can be seen in the torque curve that the design A motor develops near its full-load speed as shown in following figure.
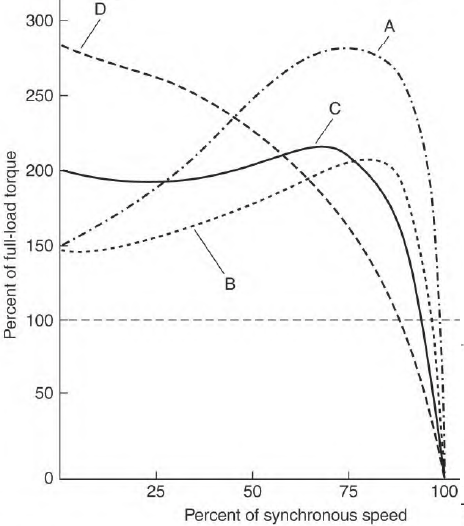
Control-Caused Motor Overheating Reasons
Duty-cycle loading requirements (that cause overheating) can be relieved by forced ventilation. Some conditions helped by forced ventilation are overheating from prolonged slow speed at maximum torque, frequent start-stop cycle, and a duty cycle that includes overloading for a short time before shutdown. Operating a motor for a time with no load will cool the winding and core uniformly. Running with no load on reduced voltage is an even better way to cool a motor.
The part-winding start method (of starting a motor) is not recommended for frequent starting.
A poorly designed variable-hertz control can cause a motor to overheat. (Voltage should change with the hertz change.) Not all motors are suited for variable-hertz drives. In many cases, older T-frame motors have not worked as well as high-efficiency motors or U-frame motors on variable hertz.
If a motor is labeled inverter duty (variable-hertz duty), it doesn’t mean the motor is designed for slow speed at maximum torque or any other extreme deviation from the motor’s speed. Inverter duty means the motor’s coil wire has special insulation. This insulation postpones breakdown from voltage spikes caused by abrupt voltage and current changes.
Heat Developing from Reduced-Power Starting
The amount of internal heat a motor accumulates in across-the-line starting compares to that produced in the wye-delta or reduced-voltage starting methods. Any reduced-power starting method that applies all the motor’s winding is better for the motor than a part-winding start method. Reducing the motor’s starting amperes lessens the amount of voltage drop caused by across-the-line starting.
In some cases, reduced-power starting is done to protect a load that is sensitive to quick starts. If a load that requires frequent starting causes the motor to heat excessively, forced ventilation will lengthen a motor’s insulation life. Ventilation should continue for a time after the motor is offline. (The amount of time required depends on the motor’s size, etc.)
For maximum motor life, it’s best to start a large motor with no load. (A clutch can be used to apply the load after the motor has reached full speed.)
Motor Fault Overheating
Shorted Turns: Shorted turns in a winding will cause overheating. When just a few coil turns are shorted, they form a closed loop. A circulating current is transformed into the loop. The current is usually high enough to melt a wire, opening the closed loop.
Before this happens, a pole forms from the circulating current in the shorted turns. This pole doesn’t conform to the surrounding poles. Its magnetism causes a ringing sound, unique to motors with shorted turns.
Shorted turns may not slow the motor at all. A line-to-line ampere comparison will show a substantial difference between motor leads, and will identify the problem as shorted turns.
Ground in Winding: If a winding is grounded (shorted) to the stator or frame, it will get hot (from the increased ampere flow). This condition usually causes a fuse or breaker to open. If there are enough coils in the motor’s circuitry between the line and the ground, the motor will still run, but with increased (and unbalanced) amperes.
Worn Bearings and Uneven Air Gap: Worn sleeve bearings cause overheating. A three-phase motor’s torque is so smooth that it may be necessary to move the shaft to detect a worn sleeve bearing. It’s common for a rotor to drag on the stator before the problem is detected. Uneven air gap from worn sleeve bearings will cause internal heating in some motors. Motors that use an internal circuit connection (that balances the current path through the poles) are less affected by uneven air gap.
Although uneven air gap should be avoided, it won’t cause immediate damage to a motor’s winding. In the past, most three-phase motors had sleeve bearings. Many ran for years with worn bearings and an uneven air gap—with no electrical problems.
Wrong Service Factor: The service factor (found on the motor’s nameplate) is the amount of overload a motor can handle (without overheating) for a limited time. The service factor number is a multiplier. The multiplier number times the motor’s nameplate amperes is the amount of overload a motor can handle. Service factor numbers are 1, 1.15, and 1.2.
A high service factor usually indicates a well-designed motor. A totally enclosed motor will have a service factor of 1, meaning it can’t be loaded higher than nameplate amperes. Many air compressors are deliberately designed to use the service factor. (They are in a highly competitive market.)
In one case, an air compressor had a 75-horsepower motor with a 1.2 service factor. The compressor was designed to use the full 1.2 service factor value. (When a compressor operates normally, it will cycle for a time unloaded so the motor has time to cool down.) Unfortunately, this motor never ran unloaded because the air volume demand was so high. The motor failed after a few months.
Connected for the Wrong Voltage: If a dual-voltage motor connected for high voltage is connected to low voltage, it will produce only one-fourth of its rated horsepower. It will start much more slowty than normal. Some loads allow this motor to reach nearly normal speed. If an induction motor’s RPM is below its nameplate rating, the high slip will cause it to overheat. If a dual-voltage motor connected for low voltage is connected to high voltage, the results with any type of load are immediate. The motor develops many times its normal starting torque, and it draws so many amperes that its winding is destroyed in a matter of seconds.
If a fully loaded motor, rated for 220 volts, is connected to 250 volts, it will run hotter than normal (a 12 percent difference). Motors with frequent start cycles will have extreme overheating problems when voltage is this high. A motor rated for 208 volts but connected to 250 volts will overheat without a load. (The connection is 20 percent over its rated voltage.)
A motor rated for 250 volts but connected to 208 volts can’t pull its rated load. It may not start a load requiring high breakaway torque. The motor will work if the load is reduced. (A tachometer should be used to make sure the RPM is not below the nameplate rating.) Any departure from rated voltage greater than +10 percent will result in extra heat.
Wrong Hertz: Motors designed for 50 Hz power most of the machinery manufactured in Europe. Problems can occur when this machinery is used in the United States on 60 Hz. A four-pole 50-Hz motor runs 300 RPM faster on 60 Hz. The motor will be overloaded if its load is air or liquid. Conveyer belts and augers will also overload this motor. (Changing the pulley dimension ratio solves the problem for some applications.) Direct-driven loads require major redesigning or replacement.
Internal Motor Problems
Internal motor problems can cause overheating.
Rotor/Stator Alignment: If the rotor and stator iron aren’t aligned properly, the result is high amperes (loaded or no load) and loss of power. This problem can’t be detected with an ohmmeter, or limited current and turning of the shaft.
Open Rotor Bars: Open rotor bars cause power loss. With a normal load, the rotor will run more slowly than the nameplate RPM, resulting in high amperes in both the rotor and the stator windings. (Too much slip increases rotor hertz, which causes higher amperes.)
Cracked End Ring: Cracked end rings cause uneven torque and loss of power. The result is similar to that of open rotor bars.
Air Gap Too Large: If the rotor becomes “out of round,” it may drag on the stator core. This condition is corrected by skimming some of the iron off the rotor with a lathe. Skimming the rotor increases the air gap.
Air gap should be kept at a minimum because it’s a break in the magnetic circuit. A large air gap creates a large increase in the motor’s magnetizing amperes. The motor will run hotter, and there will be a slight power and efficiency loss.
Whether to skim the rotor should be decided on a case-by-case basis. If the motor has more power than needed or its duty (frequent starts, etc.) doesn’t cause above-normal heating, skimming the rotor does no harm. A large air gap can be similar to a misaligned rotor. (It can’t be detected with an ohmmeter, or limited current and turning of the shaft.)
Location-Caused Overheating
In a hot location, the surrounding air increases a motor’s normal running temperature. If the motor is loaded near its capacity, it will overheat. Even forced ventilation may not help. If a motor is located too close to a wall or if anything impedes its intake or exhaust airflow, it can overheat (depending on ambient temperature). The recommended clearance is 18 inches on all sides.
Intense sunlight can cause a maximum-loaded motor (or a motor that starts frequentty) to overheat. An enclosure added for protection from the weather can be harmful to a motor, because air movement is restricted. In addition, the enclosure may trap the motor’s hot air exhaust. An exhaust fan is often added to remove the hot air from the enclosure. However, forced air movement shouldn’t affect the motor’s normal air movement.
Maintenance-Caused Overheating
Belts Too Tight: Extra stress is put on bearings if the belts are too tight. If the motor has a long stator, the shaft may bow and misalign the bearing’s inner race. There have been cases where the rotor dragged on the stator core (because of overly tightened belts).
Pulley Problems: A replacement pulley that is slightly larger than the original can overload a motor if the load increases with a speed increase. A worn pulley may make it necessary to tighten the v-belts excessively (to keep them from slipping).