There are many ways to measurement of a physical quantity. While the selection of transducers, and how to select a transducer for a particular application, the following points should be kept in the mind.
Unfortunately, most transducers are not sensitive to just one quantity. If measurements are to be made under conditions where there is a likelihood of two or more input quantities influencing the transducer, it is desirable to select a transducer that is sensitive to the desired quantity and insensitive to the unwanted quantity. If this is not possible, ways and means should be found to eliminate or compensate for the effects of the unwanted input quantity.
Selection Criteria of Transducer
1. Operating Principle: The transducers are many times selected based on the operating principle used by them. The operating principles used may be resistive, inductive, capacitive, optoelectronic, piezoelectric, etc.
2. Sensitivity: The transducer must be sensitive enough to produce detectable output.
3. Operating Range: The transducer should maintain the range requirements and have a good resolution over its entire range. The rating of the transducer should be sufficient so that it does not break down while working in its specified operating range.
4. Accuracy: A high degree of accuracy is assured if the transducer does not require frequent calibration and has a small value for repeatability. It may be emphasized that in most industrial applications, repeatability is considerably more important than absolute accuracy.
5. Cross sensitivity: Cross sensitivity is a further factor to be taken into account when measuring mechanical quantities. There are situations where the actual quantity measured is in one plane and the transducer is subjected to variations in another plane.
More than one promising transducer design has had to be abandoned because the sensitivity to variations of the measured quantity in a plane perpendicular to the required plane has been such as to give completely erroneous results when the transducer has been used in practice.
6. The transducer should maintain the expected input-output relationship as described by its transfer function to avoid errors in transducers.
7. Transient and Frequency Response: The transducer should meet the desired time domain specifications like peak overshoot, rise time, settling time, and small dynamic error. It should ideally have a flat frequency response curve. In practice, however, there will be cutoff frequencies and higher cut-off frequencies should be high to have a wide bandwidth.
8. Loading Effects: The transducer should have a high input impedance and a low output impedance to avoid loading effects.
9. Environmental Compatibility: It should be assured that the transducer selected to work under specified environmental conditions maintains its input-output relationship and does not break down. For example, the transducer should remain operable under its temperature range. It should be able to work in corrosive environments (if the application so requires) and should be able to withstand pressures, shocks, and other interactions to which it is subjected.
10. Insensitivity to Unwanted Signals. The transducer should be minimally sensitive to unwanted signals and highly sensitive to desired signals.
11. Usage and Ruggedness. The ruggedness both of the mechanical and electrical intensities of the transducer versus its size and weight must be considered while selecting a suitable transducer.
14. Electrical aspects. The electrical aspects that need to be considered while selecting a transducer include the length and type of cable required. Attention also must be paid to the signal-to-noise ratio in case the transducer is to be used in conjunction with amplifiers. Frequency response limitations must also be taken into account.
15. Stability and Reliability: The transducer should exhibit a high degree of stability to be operative during its operation and storage life.
16. Static Characteristics: Apart from low static error, the transducers should have a low non-linearity low hysteresis, high resolution, and a high degree of repeatability.
The transducer selected should be free from load alignment effects and temperature effects. It should not need frequent calibration, should not have any component limitations, and should be preferably small in size.
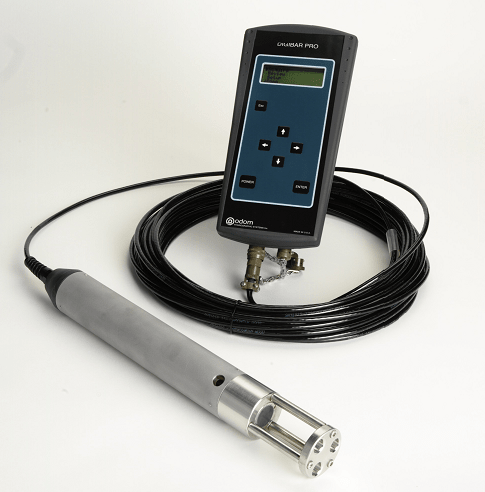
Selection Criteria of Transducer
While choosing a transducer for any application the input characteristics, output characteristics, and transfer characteristics have to be taken into account.
1. Input Characteristics
(i) Type of Input and Operating Range: The foremost consideration for the choice of a transducer is the input quantity it is going to measure and its operating range. The type of input, which can be any physical quantity, is generally determined in advance. A physical quantity may be measured by the use of several transducers. However, the choice of a particular transducer that is selected for the purpose, depends upon the useful range of input quantity over which the transducer can be used.
The operating range of the transducer may be a decisive factor in the selection of a transducer for a particular application. The upper limit is decided by the transducer’s capabilities while the lower limit of the range is normally determined by the transducer error or by the unavoidable noise originating in the transducer. The transducer should maintain a good resolution throughout its operating range.
(ii) Loading Effects: Ideally, a transducer should have no loading on the input quantity being measured. In theory, it is impossible, although in practice steps may be taken to reduce the loading effects to negligible proportions.
The magnitude of the loading effects can be expressed in terms of force, power, or energy extracted from the quantity under measurement for the working of the transducers.
Therefore, the transducer, that is selected for a particular application should ideally extract no force, power, or energy from the quantity under measurement so that the latter is measured accurately.
2. Output Characteristics
The three conditions in the output characteristics which should be considered are
- type of electrical output,
- output impedance, and
- useful range.
(i) Type of Electrical Output: The types of output which may be available from the transducers may be a voltage, current, impedance, or a time function of these amplitudes. These output quantities may or may not be acceptable to the latter stages of the instrumentation system.
They may have to be manipulated i.e. their magnitudes changed or they may have to be changed in their format by signal conditioning equipment to make them drive the subsequent stages of the instrumentation system.
(ii) Output Impedance: The output impedance, Zo, of a transducer determines to the extent the subsequent stages of instrumentation are loaded. Ideally, the value of output impedance should be zero if no loading effects are there on the subsequent stage.
However, the output impedance, Z0, cannot be made equal to zero and therefore, its value should be kept as low as possible to minimize the loading effects. The output impedance determines the amount of power that can be transferred to the succeeding stages of the instrumentation system for a given output signal level.
If the output impedance is low compared to the forward impedance of the system, the transducer has the characteristics of a constant voltage source (provided the output of the transducer is a voltage), while in case the forward impedance is high as compared with the output impedance of transducer, it behaves as a constant current source.
When the output impedance of the transducer is equal to that of the following stages of the instrumentation system, matching takes place and the maximum power is transferred from the transducer to the succeeding stages.
(iii) Useful Output Range: The output range of a transducer is limited at the lower end by noise signal which may shroud the desired input signal. The upper limit is set by the maximum input level. The output range can be increased, in some cases, by the inclusion of an amplifier in the transducer.
However, the inclusion of an amplifier also increases the noise level, and therefore in such situations, the amplifier may not be of any use at all.
3. Transfer Characteristics
The transfer characteristics of transducers require the attention of three separate elements, viz,
- transfer function
- error, and
- response of the transducer to environmental influences.
(i) Transfer Function: The transfer function of a transducer defines a relationship between the input quantity and the output.
The transfer function is, qo = f(qi)
Where qo and qi, are respectively output and input of the transducer.
The sensitivity of a transducer is defined as the differential quotient,
S = dqo/dqi
In general, the sensitivity of transducers is not constant but is dependent upon the quantity qi. However, in some cases the relationship between the output qo, and input qi, is linear.
In that case, the sensitivity remains constant over the entire range of the transducer and is defined as,
S’ = dqo/dqi = qo/qi
The scale factor is defined as the inverse of sensitivity and is, therefore,
scale factor = 1/S = dqi/dqo
Some manufacturers specify the scale factor and still call it sensitivity.
(ii) Response of Transducer to Environmental Influences: The response of the transducer to environmental influences is of great importance. This is often given insufficient attention when choosing the best transducer for a particular application. This gives rise to inaccurate results.
The performance of the transducer is fully defined by its transfer function and errors provided that the transducer is in a constant environment and subject to any disturbances like stray electromagnetic field and electrostatic fields, mechanical shocks and vibration, temperature changes, pressure and humidity changes, change in supply voltages and improper mechanical mountings.
If transducers are subjected to these environmental disturbances, precautions are taken, to get an error-free result.
Thanks for reading about “selection criteria of transducer”.
The concept of smart transducers that integrate sensing with data processing is exciting. Proact, founded in 2001 and based in Bengaluru, is a leading force in high-tech industries like aerospace, aviation, electronics, defense, and more. Renowned for innovation and excellence, Proact offers tailored solutions to diverse challenges, making it a trusted partner for businesses. Explore cutting-edge services and products at https://www.proact-ims.com/ or contact us at +91 80 3542 9949 for collaboration and innovation opportunities.
I’m working on a DIY project that requires transducers, and your tips on selecting the right one were super helpful! Can’t wait to put them into practice!. Proact, founded in 2001 and based in Bengaluru, is a leading force in high-tech industries like aerospace, aviation, electronics, defense, and more. Renowned for innovation and excellence, Proact offers tailored solutions to diverse challenges, making it a trusted partner for businesses. Explore cutting-edge services and products at https://www.proact-ims.com/ or contact us at +91 80 3542 9949 for collaboration and innovation opportunities.
Can you do a follow-up post on electric vehicle maintenance solutions? That’s something many of us are curious about. Discover innovative services and products at https://www.proact-ims.com/ or reach out at +91 80 3542 9949 for collaboration and growth opportunities.