Synchronous motors have their pole-shoes slotted for placing copper bars. The copper bars are placed in these slots and short-circuited at both ends by heavy copper rings (like squirrel cage rotor of induction motors). This arrangement is known as damper winding in synchronous motor.
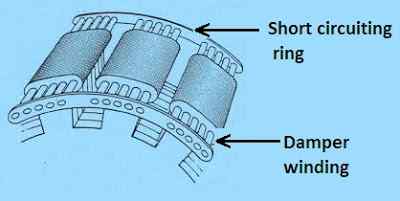
Role of Damper Winding in Synchronous Motor
The damper winding in synchronous motor performs two functions:
- provides starting torque and
- prevents hunting in the synchronous motor
When the rotor is rotating at synchronous speed, then the relative velocity between the RMF (rotating magnetic field of the stator) and the rotor is zero. Hence induced EMF in the damper winding is zero.
Thus, under normal running conditions, damper winding in synchronous machine does not carry any current.
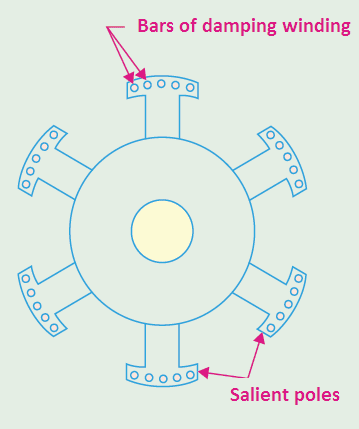
Hunting in Synchronous Motor
The stator and the rotor poles of running synchronous motor are magnetically locked and, hence, both run with the same synchronous speed. But centerlines of the two poles do not coincide with each other. The rotor slips back behind the stator poles by a small angle δ.
This angle is known as the load angle or torque angle. This backward shift of the rotor is essential for developing motor torque.
As the load on the motor is increased, the backward shift of rotor poles increases by a larger angle, but rotor poles still continue to run synchronously. The value of load angle δ depends on the load carried by the motor. This load angle also controls the stator current.
Greater will be the value of δ; higher will be the value of stator armature current. It is so because the motor needs more input power to carry the increased load. If too much load is put on a synchronous motor, the rotor will be pulled out of synchronism, and it will stop.
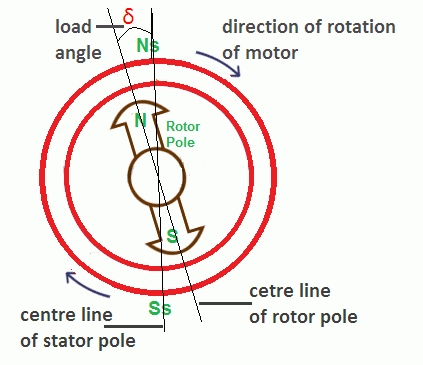
If the load on the motor is increased gradually, then the rotor goes to a new position smoothly. But if the motor load is changed suddenly, then the rotor cannot get its new position corresponding to the new value of δ smoothly. Due to inertia, the rotor oscillates around its correct position for some time before coming to the correct position. It is known as hunting in synchronous motor.
- Due to hunting, the value of δ changes continuously.
- Due to change in δ, the back EMF Eb changes which forces the armature current Ia to change continuously.
- This continuously varying armature current will cause problems to the other appliances connected on the same AC line.
- If the load changes are frequent, then the rotor swings about its new position due to inertial.
- If the frequency of oscillations matches the natural frequency of the motor, then the amplitude of rotor swings increases, and the motor may be thrown out of synchronization.
The damper winding in synchronous motor plays a very important role in hunting. When the rotor oscillates, the relative motion between RMF and the rotor becomes nonzero. Hence an EMF is induced proportional to relative motion in damper winding. This induced EMF is in such a direction that it will try to oppose the cause of it (Lenz’s law). Here the cause is relative motion due to hunting. Hence the hunting reduces quickly due to damper winding.
The time taken by the rotor to reach its final equilibrium position after hunting is known as ‘settling time’. It should be as short as possible. The use of damper winding in synchronous motor reduces its settling time considerably.
Damper Winding in Synchronous Generator
The hunting can also occur in a synchronous generator. In this case also, due to sudden change in electrical output or mechanical input, oscillations are set up in the rotor called hunting, which can be prevented by providing damper winding in synchronous generator.
Thanks for reading about “damper winding in synchronous motor”.