Hi friends,
In this article, I am discussing the “Creep in materials.” Types of creep and creep strength. So let us start.
Metals will deform under steady service loads less than the short-time elastic strength if the loads are applied for a very long time at temperatures near the crystallization temperature. Apparently, the atoms tend to flow in the direction of the load and, the deformation becomes significant. Greater stress, temperature, and time will actually cause fracture. This phenomenon is referred to as creep.
What is creep in materials?
Creep may be defined as the slow and progressive deformation of a material with time under a constant stress. The phenomenon of creep is observed in metals, ionic and covalent crystals and amorphous materials such as glasses and high polymers, metals, except for a few exceptions like lead, exhibit creep at high temperature whereas amorphous materials like rubber, plastic, and the like are very temperature-sensitive to creep.
What is importance of creep?
Creep becomes important in the following cases:
- Soft metals employed at about room temperature such as lead pipes and white metal bearings.
- Steam and chemical plants operating at 450 — 550°C.
- Gas turbines working at high temperatures.
- Rockets and missiles, supersonic jets.
- Nuclear reactor field.
What are types of creep?
Creep occurs at stresses well below the elastic limit at elevated temperatures. Whether a given temperature is “elevated” or not depends on the material because one material may creep more at room temperature than another say at 1000°C. It is, therefore, best to study the behavior of creep and define their types at different ranges of temperature. The creep may, therefore, be categorized depending on the temperature,
- as the logarithmic creep,
- the recovery creep,
- and the diffusion creep or plastic creep.
At low temperature the creep rate usually comes down with time and logarithmic creep curve is obtained. The deformation caused is proportional to time. At higher temperatures in the range of 0.5 to 0.7 of the melting point Tm measured on the absolute scale in K, however, the influence of work-hardening is weakened and there is a possibility of mechanical recovery. Consequently, the creep rate does not drop as rapidly as at low temperature.
High temperature creep which occurs in many engineering materials particularly during the hot working of metals falls under this category. At very high temperature, i.e., beyond 0.7 TmK the creep is primarily influenced by diffusion and the stress applied has little effect.
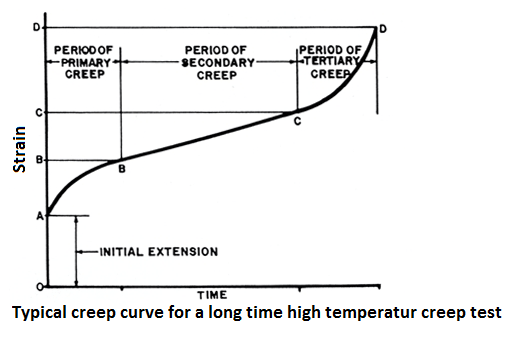
Creep curve depicted in Figure illustrates the variation of the extension of a metal with time under different stresses. This curve is for a constant nominal stress and constant temperature. It shows three distinct stages of creep:
- primary creep,
- secondary creep, and
- tertiary creep.
The first stage of creep, called the primary creep, represents a region of a decreasing creep rate. Primary creep is a period of pure dominantly transient creep in which the creep resistance of the material increases by virtue of its own deformation. For low temperatures and stresses, as in the creep of load at room temperature, primary creep is the predominant creep process.
The second stage of creep, called the secondary creep, is a period of nearly constant creep rate which results from a balance between the work hardening process and recovery. This is the reason that the secondary creep is usually called the steady-stage creep. The average value of the creep rate during secondary creep is referred to as the minimum creep rate. This is the significant portion of the curve for most applications.
The third stage of creep or tertiary creep mainly occurs at an accelerated rate. It actually represents a process of progressive damage resulting in an imminent fracture of the material through inter-crystalline or other causes.
Creep Strength
Creep strength is the constant nominal stress that will cause a specified creep extension in a given time at a constant temperature. This can be had by drawing the creep curve for the metal or alloy. The permissible amounts of creep depend largely on the article and service conditions.
Factors Affecting Creep in Materials
Creep is much more affected by grain size, micro-structure and previous strain history, for instance, cold work, than many other factors. Grain size is a major factor in creep. Coarse-grained materials exhibit better creep resistance than fine-grained ones, as fine-grained metals have a greater amount of grain boundary materials and grain boundaries behave as a quasi-viscous material with a high tendency to flow at elevated temperatures. That is why single crystals exhibit a higher creep resistance than poly-crystalline materials. Since tungsten filaments of electrical lamps are made of single crystals, they can withstand very high temperatures.
The next important factor is the thermal stability of the micro-structure of alloys and its resistance to oxidation at high temperatures. An annealed specimen, for instance, for having greater thermal stabilities is far superior in its creep resistance to quenched steel for its poor thermal stability.
Cold working has also a strong effect on creep which is accelerated in some metals during re crystallization following cold work. This accelerated creep is followed by a period of relatively slow creep in the recrystallized metal.
Pure metals which have high melting points and compact atomic structure usually show good creep resistance at high temperatures. The creep resistance of pure metals can be considerably increased by alloying them with suitable elements.
Fatigue
Fatigue occurs because of the formation of fractures on the surface of the sample. Each time the load is applied, the small fractures grows in size by a small amount until it breaks. Fatigue is very important in applications where large varying forces are applied to materials as in hydraulic presses and rams.
Thanks for reading about ‘What is creep in material science?’
Related Posts
- Dia Para Ferro Magnetic Materials
- Applications of Soft and Hard Magnetic Materials
- Why CRGO core is used in transformers?
- Properties of High Resistivity Materials
- Properties of Insulating Materials
- Applications of Insulating Materials
- Properties of Superconductors
- Dielectric Strength | Constant | Loss | Definition
- Creep in Materials